-
The procedures in Appendix RA3.2 are for use for residential air-cooled air conditioners and air-source heat pumps to verify the systems have the required refrigerant charge.
-
For dwelling units with multiple air conditioners or heat pumps, the procedures shall be applied to each system separately.
-
Appendix RA3.2 defines two procedures, the Standard Charge Verification Procedure in Section RA3.2.2 and the Weigh-in Charging procedure in Section RA3.2.3.
-
Sections 150.1(c)7 and 150.2(b)1F specify the requirements for minimum system airflow rates to be verified in conjunction with the refrigerant charge verification.
-
Failure to follow the manufacturer’s installation and charging instructions may result in significant refrigeration system faults that may invalidate refrigerant charge and metering device verification results. The installer shall certify that he/she has conformed to the manufacturer’s instructions and specifications for charging the system prior to proceeding with the verification procedures in this appendix.
-
In the case where the Energy Commission has approved an alternative protocol as described in RA1, the HVAC Installer and HERS Rater may choose to perform the alternative refrigerant charge verification procedure.
- The procedures in Section RA3.2.2 are applicable to ducted split system air-cooled air conditioners and ducted split system air-source heat pumps, and may be applicable to packaged air-cooled air conditioners and packaged air-source heat pumps.
- The procedures in Section RA3.2.2 require verification of the applicable minimum system airflow rate across the cooling coil when refrigerant charge is verified.
- The procedures in Section RA3.2.2 require verification (for applicable systems) that the metering device is operating properly.
- The procedures in Section RA3.2.2 may be used when the outdoor air temperature is 55°F or above.
- When refrigerant charge verification is required for compliance, the applicable procedures in Section RA3.2.2 shall be used by the HVAC installer after installing a new HVAC system or after altering refrigerant-containing components in an existing HVAC system, and after charging the air conditioner or heat pump system in accordance with the manufacturer's instructions and specifications.
- The applicable procedures in Section RA3.2.2 shall always be used by the HERS Rater for verification of the system's refrigerant charge when HERS verification is required for compliance unless an applicable alternate procedure is available in Reference Residential Appendix RA1, or the Standards specify the Section RA3.2.3.2 procedure (observation of weigh-in) as mandatory for compliance, or as an available option for compliance and the HVAC installer elects to use the RA3.2.3.2 procedure for HERS verification.
- When the procedures in Section RA3.3.3.1.5 (alternative to compliance with minimum system airflow) are utilized for compliance, HERS verification compliance shall not use group sampling.
- The procedures in Section RA3.2.3 are applicable to air-cooled air conditioners or air-source heat pumps.
- The weigh-in charging procedure is an acceptable method for demonstrating compliance at any outdoor temperature.
- Use of the Section RA3.2.3 procedure does not exempt the system from compliance with all applicable minimum airflow rate verification requirements.
- When the procedures in Section RA3.2.3 are utilized by the HVAC installer, HERS verification compliance shall not use group sampling.
- The procedures in Section RA3.2.3.1 shall be used by HVAC installers when refrigerant charge verification is required for compliance when the outdoor air temperature is below 55°F, and there is no applicable alternative refrigerant charge verification protocol in Reference Residential Appendix RA1 available for use with the system for outdoor temperatures below 55°F.
- The procedures in Section RA3.2.3.1 shall be used by HVAC installers when refrigerant charge verification is required for compliance when the standard charge verification procedure in RA3.2.2 is not applicable to the system that must demonstrate compliance, and there is no applicable alternative refrigerant charge verification protocol in Reference Residential Appendix RA1 available for use with the system.
- The procedures in Section RA3.2.3.1 shall not be utilized by HERS Raters for verification of refrigerant charge.
- The procedures in Section RA3.2.3.2 shall be utilized by HERS Raters for verification of refrigerant charge only when the Standards specify that the Section RA3.2.3.2 procedure shall be used for HERS verification compliance, otherwise only when the Standards specify the RA3.2.3.2 procedure is an available option, and the HVAC installer elects to use the RA3.2.3.2 procedure for HERS verification compliance.
This section specifies the standard charge verification procedure. Under this procedure, the refrigerant charge is verified using the "superheat charging method" for systems with fixed metering devices, or the "subcooling charging method" for systems with thermostatic expansion valves (TXV) or electronic expansion valves (EXV).
The following sections describe the required instrumentation; required calibration for the instrumentation; required diagnostic measurements; and the required calculations to determine results that must be compared to the criteria in Table RA3.2-1 to determine compliance.
Refrigerant charge verification utilizing the procedures in Section RA3.2.2 requires compliance with a minimum airflow rate across the cooling coil at the time of charge verification, as specified by Standards Sections 150.1(c)7Aib and 150.2(b)1Fiia as applicable.
Table RA3.2-1 summarizes the standard charge verification protocols and defines the corresponding compliance criteria that shall be used by system installers and HERS Raters.
Case | User Application | Compliance Criteria | Procedure(s) |
Standard Charge Verification Procedure - Fixed Metering Device Systems | Installer Testing at Final | 55°F ≤ Outdoor Air Dry-bulb Temp ≤ 115°F Return Air Dry-bulb Temp ≥ 70°F Return Air Wet-bulb Temp ≤ 76°F Superheat tolerance ±5°F of the specified target | |
Standard Charge Verification Procedure - Fixed Metering Device Systems | HERS Rater Testing | 55°F ≤ Outdoor Air Dry-bulb Temp ≤ 115°F Return Air Dry-bulb Temp ≥ 70°F Return Air Wet-bulb Temp ≤ 76°F Superheat tolerance±8°F of the specified target | |
Standard Charge Verification Procedure - Variable Metering Device Systems | Installer Testing at Final | 55°F ≤ Outdoor Air Dry-bulb Temp ≤ 120°F Return Air Dry-bulb Temp ≥ 70°F Subcooling tolerance ±3°F of the manufacturer-specified target1 Metering Device tolerance: Superheat meets the Manufacturer's specifications or 4°F ≤ Superheat ≤ 25°F | |
Standard Charge Verification Procedure - Variable Metering Device Systems | HERS Rater Testing | 55°F ≤ Outdoor Air Dry-bulb Temp ≤ 120°F Return Air Dry-bulb Temp ≥ 70°F Subcooling tolerance ±6°F of the manufacturer-specified target1 and Subcooling ≥2°F Metering Device tolerance: Superheat meets the Manufacturer's specifications or 3°F ≤ Superheat ≤ 26°F |
Note:
1. If a manufacturer-specified subcooling target value is not available or cannot be determined, the Executive Director may provide additional guidance for compliance.
The standard charge verification procedure detailed in this section may be used to demonstrate compliance when the outdoor temperature is within the manufacturer's specified temperature range, or the outdoor temperature is 55°F or higher, after the HVAC installer has installed and charged the system in accordance with the manufacturer’s specifications. The return dry bulb temperature shall be maintained above 70°F during the test.
This procedure does not relieve the installing contractor from any obligation to conform to the manufacturers’ specifications for installation, refrigerant charge, or system operation. This procedure is used to determine compliance with Title 24, Part 6.
Persons who use this procedure to demonstrate compliance with Title 24 Part 6 shall be qualified to perform the following:
- Obtain accurate system pressure and saturation temperature readings utilizing digital refrigeration gauges.
- Obtain accurate temperature readings utilizing a digital thermometer and temperature sensors.
- Check calibration of digital refrigerant gauges using a known reference pressure.
- Check calibration of digital thermometer and temperature sensors using a known reference temperature.
- Determine the required or best location for temperature measurements in duct systems and on refrigerant lines.
- Calculate the measured superheat and subcooling.
- Determine the required superheat, based on the conditions present at the time of the test.
- Determine if measured values are accurate.
Instrumentation for the procedures described in this section shall conform to the following specifications:
Temperature measurements shall be made utilizing digital temperature measurement instrumentation (combined sensor plus device for data acquisition, processing and reporting) that shall have dual channel capability in Celsius or Fahrenheit and conform to the following specifications:
Air temperature measurements made of supply or return airflow and the outdoor air entering the condensing unit shall meet the following specifications:
- Accuracy: ± 2°F.
- Resolution: 0.2°F.
Air temperature measurements made of return airflow using the wetted wick method shall use a temperature sensor and a clean cotton wick wetted with distilled water. Temperature measurements using this method shall meet the following specifications:
- Accuracy: ± 2°F.
- Resolution: 0.2°F.
Air temperature measurements made of return airflow using a digital hygrometer device shall have a probe that is a minimum of 3 inches in length, and be capable of measurements for both dry-bulb and wet-bulb temperature. Dry-bulb and wet-bulb temperature measurements made with digital hygrometer devices shall meet the following specifications:
- Accuracy: ± 2°F wet-bulb temperature; or a calculated wet-bulb temperature based on accuracies of ± 3% RH and ± 2.0 degree F Dry bulb temperature.
- Resolution: 0.2°F.
Temperature measurement of suction or liquid refrigerant lines using sensor mounting styles such as pipe-clamp sensors, Velcro strap-on, or an equivalent sensor device or sensor mounting method shall meet the following specifications:
- Accuracy: ± 2°F.
- Resolution: 0.2°F.
Measurements for verification of refrigerant charge require air temperature sensors that pass the following qualifying test:
-
Using a test enclosure or test environment that is maintained at known dry bulb temperature T1;
-
The temperature sensor subjected to the qualifying test shall be placed outside the test enclosure or test environment until its temperature has stabilized at a drybulb temperature T2;
-
The absolute value of (T1 minus T2 ) shall be greater than 40ºF; and
-
The sensor shall have a response time that produces the accuracy specified in Section RA3.2.2.2.1 within 90 seconds of insertion into the test enclosure or test environment.
Measurements for verification of refrigerant charge require two (2) pipe temperature sensors that pass the following qualifying test:
-
Using test pipes in six sizes (1/4” dia., 3/16” dia., 3/8” dia., 3/4” dia., 7/8” dia., 1 1/8” dia.) that are maintained at a known temperature T1 in a test enclosure or test environment that is maintained at a known dry-bulb temperature T2;
-
The absolute value of (T1 minus T2 ) is greater than 40ºF;
-
The temperature sensor subjected to the qualifying test shall be placed in the test enclosure or test environment until its temperature has is stabilized at T2;
-
The sensor shall have a response time that produces the accuracy specified in Section RA3.2.2.2.1.4 within 90 seconds of application of the sensor to one of the test pipes; and
-
A sensor may be used for more than one pipe size if it passes the above test for each pipe size for which it is used.
Refrigerant pressure measurements shall be made utilizing digital measurement instrumentation. Measurements made with digital refrigerant pressure measurement devices shall meet the following specifications
-
Accuracy: ± 7.0 psi liquid line pressure
-
Accuracy: ± 3.5 psi suction pressure
As an alternative, two saturation pressure measurement sensors (SPMS) may be permanently installed by the equipment manufacturer, or in a manner and location approved by the equipment manufacturer for use for measuring the saturation pressure of the refrigerant in the evaporator coil and in the condenser coil. Refer to Reference Joint Appendix JA6.2 for additional specification for SPMS.
When required for compliance by Standards Section 150.1(c)7Aia, or when return plenum measurements are necessary for compliance with refrigerant charge verification requirements, a 5/8 inch (16 mm) diameter hole shall be provided as shown in Figure RA3.2-1.
Return plenum temperature measurements shall be taken at the location specified in Figure RA3.2-1 when performing the procedures in RA3.2. The measurement access shall be sealed to prevent leakage after the measurements have been completed.
The hole location shown in Figure RA3.2-1 can be applied to any one of the four sides of the return plenum. The hole location shall be labeled "Title 24 – Return Plenum Measurement Access" in at least 12-point type.
For air-handling units with the return located entirely within conditioned space (such as when an up-flow air handler is mounted on a pedestal in a closet in the dwelling, or when the return grille is an integral part of the air-handling unit), the return plenum measurement access hole is not required, and in this case the return air temperature measurements shall be taken at the return grill when performing the procedures in RA3.2.
Systems that cannot conform to the specifications for the hole location shown in Figure RA3.2-1 shall not be required to have holes as described in Figure RA3.2-1; however if return plenum measurements are required for compliance, an alternate location that provides access for making an accurate return plenum measurement shall be used.
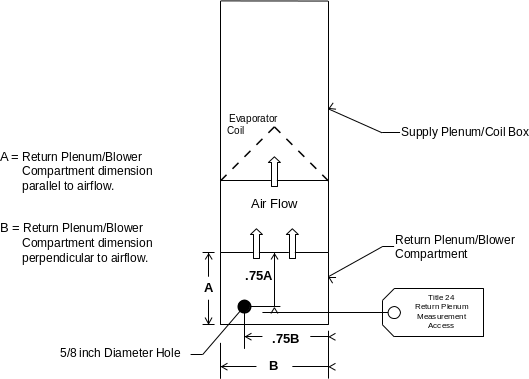
Figure RA3.2-1 Measurement Access Hole
The accuracy of instrumentation shall be maintained using the following procedures. A sticker with the calibration check date shall be affixed to each instrument calibrated.
Thermometers with their temperature sensors shall be calibrated monthly to ensure that they are reading accurate temperatures.
The following procedure shall be used to check thermometer/temperature sensor calibration:
- Fill an insulated cup (foam) with crushed ice from distilled water. The ice shall completely fill the cup. Add distilled water to fill the cup.
- Insert two sensors into the center of the ice bath and attach them to the digital thermometer.
- Let the temperatures stabilize. The temperatures shall be 32 degrees Fahrenheit (plus or minus 1 degrees Fahrenheit). If the temperature is off by more than 1 degrees Fahrenheit make corrections according to the manufacturer’s instructions. Any sensors that are off by more than 2 degrees Fahrenheit shall be replaced.
- Switch the sensors and ensure that the temperatures read on both channels are still within plus or minus 1 degrees Fahrenheit of 32 degrees Fahrenheit.
- Affix sticker with calibration check date onto sensor.
- Repeat the process for all sensors.
Refrigerant gauges shall be checked monthly to ensure that the gauges are reading the correct pressures and corresponding temperatures. The following procedure shall be used to check gauge calibration:
- Place a refrigerant cylinder in a stable temperature environment and let it acclimate for 4 hours minimum to stabilize to the ambient conditions.
- Attach a calibrated temperature sensor to the refrigerant cylinder using tape so that there is good contact between the cylinder and the temperature sensor.
- Insulate over the temperature sensor connection to the cylinder.
- Zero the low side and high side refrigerant gauges with all ports open to atmospheric pressure (no hoses attached).
- Re-install the hoses, attach the high side gauge to the refrigerant cylinder, and open the valves to measure the pressure in the refrigerant cylinder.
- Read the temperature of the sensor on the refrigerant cylinder.
- Using a pressure/temperature chart for the refrigerant, look up the pressure that corresponds to the temperature measured.
- If gauge does not read the correct pressure corresponding to the temperature, the gauge is out of calibration and needs to be recalibrated.
- Close the valve to the refrigerant cylinder, and bleed off a small amount of refrigerant to lower the high side pressure to give a corresponding temperature to between 45°F and 55°F.
- Open the valves between the high side gauge and low side gauge.
- If the two gauges corresponding refrigerant temperatures do not read within 1°F of each other, the low side gauge is out of calibration and needs to be recalibrated.
- Affix sticker with calibration check date onto refrigerant gauge.
Digital hygrometers shall be calibrated according to the manufacturer's recommended procedures. When the manufacturer certifies the calibration for a limited time, the digital hygrometer shall be recalibrated according to the manufacturers required procedure when the calibration period expires.
The following procedure shall be used to obtain measurements necessary to verify the required refrigerant charge.
-
Follow the manufacturer’s directions and adhere to the manufacturer's limitations on indoor ambient air temperature (Tindoor air) and outdoor ambient air temperature (Toutdoor air) applicable to this procedure. Ensure that the return air dry bulb temperature remains equal to or greater than 70°F prior to and while performing the measurements.
-
Verify that a liquid line filter drier has been installed if required per outdoor condensing unit manufacturer's instructions, and installed with the proper orientation with respect to refrigerant flow, if applicable.
-
Connect the refrigerant gauges to the service ports, taking normal precautions to not introduce air into the system.
-
Attach one pipe temperature sensor to the suction line near the suction line (low side) service valve and attach one pipe temperature sensor to the liquid line near the liquid line (high side) service valve. The sensors should be positioned to make good contact with the surface of the refrigerant line.
-
Attach a temperature sensor to measure the condenser entering air dry-bulb temperature. The sensor shall be placed so that it records the average condenser air entering temperature and is shaded from direct sun.
-
Insert a dry-bulb temperature sensor into the return plenum at the "Title 24 – Return Plenum Measurement Access" detailed in Section RA3.2.2.3.
-
Be sure that all cabinet panels that affect airflow are in place before making measurements. The temperature sensors shall remain attached to the system until the final charge is determined.
-
Operate the air conditioner in cooling mode for 15 minutes to allow the temperatures and pressures to stabilize before taking any measurements. While the system is stabilizing, proceed with setting up the remaining temperature sensors if used.
-
If used, place the cotton wick wet-bulb temperature sensor in distilled water, and ensure it is saturated. Do not get the dry-bulb temperature sensors wet.
-
If the system has a fixed metering device, at 12 minutes, insert a wet-bulb temperature sensor into the return plenum at the "Title 24 – Return Plenum Measurement Access" detailed in Section RA3.2.2.3.
-
If the system has a fixed metering device, after the system has operated for 15 minutes, and when the return plenum wet-bulb temperature has stabilized, using the temperature sensor already in place, measure and record the return (evaporator entering) air wet-bulb temperature (Treturn, wb).
-
Using the temperature sensor already in place, measure and record the return (evaporator entering) air dry-bulb temperature (Treturn, db).
-
Using the refrigerant gauge or saturation pressure measurement sensor already attached, measure and record the suction line (low side) pressure, and record the refrigerant saturation temperature corresponding to the measured low side pressure (Tevaporator, sat).
-
Using the refrigerant gauge or saturation pressure measurement sensor already attached, measure and record the liquid line (high side) pressure, and record the refrigerant saturation temperature corresponding to the measured high side pressure (Tcondenser, sat).
-
Using the pipe temperature sensor already in place, measure and record the suction line temperature (Tsuction,).
-
Using the pipe temperature sensor already in place, measure and record the liquid line temperature (Tliquid).
-
Using the dry-bulb temperature sensor already in place, measure and record the condenser (entering) air dry-bulb temperature (Tcondenser, db).
The above measurements shall be used to verify the refrigerant charge as described in following sections.
The following steps describe the calculations to determine if the system meets the required refrigerant charge and metering device function using the measurements determined in Section RA3.2.2.5. If a system fails, then remedial actions must be taken by the HVAC system installer. Be sure to run the air conditioner for 15 minutes after the final adjustments before taking any measurements.
The Superheat Charging Method is used only for systems equipped with fixed metering devices. These include capillary tubes and piston-type metering devices.
- Calculate Actual Superheat as the suction line temperature minus the evaporator saturation temperature.
Actual Superheat = Tsuction, – Tevaporator, sat - Determine and record the Target Superheat using Table RA3.2-2 or the manufacturer's superheat chart using the return air wet-bulb temperature (Treturn, wb) and condenser air dry-bulb temperature (Tcondenser, db).
- If a dash mark is read from Table RA3.2-2, the target superheat is less than 5°F. Note that a valid refrigerant charge verification test cannot be performed under these conditions. A severely undercharged unit will show over 9°F of superheat. However overcharged units cannot be detected from the superheat method under these conditions. The usual reason for a target superheat determination of less than 5°F is that outdoor conditions are too hot and the indoor conditions are too cool. One of the following is needed so a target superheat value can be obtained from Table RA3.2-2 either
- turn on the space heating system and/or open the windows to warm up indoor temperature; or
- retest at another time when conditions are different.
- Calculate the difference between actual superheat and target superheat (Actual Superheat - Target Superheat).
- In order to allow for inevitable differences in measurements, the Pass/Fail criteria are different for the Installer and the HERS Rater.
- For the Installer, if the difference is within the tolerance given as compliance criteria in Table RA3.2-1, then the system passes the required refrigerant charge criterion.
- For the HERS Rater inspecting the system, if the difference is within the criteria in Table RA3.2-1, then the system passes the required refrigerant charge criterion.
- For the Installer, if the system fails to meet the criteria, refrigerant needs to be added if the superheat is too high and refrigerant needs to be removed if it is too low. The installer needs to remain aware of other potential system faults. Adjust refrigerant charge and check the measurements as many times as necessary to pass the test. After the final adjustment has been made, allow the system to run 15 minutes before completing the final measurement procedure.
The Subcooling Charging Method is used for systems equipped with variable metering devices. These include Thermostatic Expansion Valves (TXV) and Electronic Expansion Valves (EXV). The amount of refrigerant is set based on the measured subcooling value, and the measured superheat value determines whether the metering device is working properly.
- Calculate Actual Subcooling as the condenser saturation temperature minus the liquid line temperature. Actual Subcooling = Tcondenser, sat – Tliquid.
- Determine the Target Subcooling specified by the manufacturer.
- Calculate the deviation of the actual subcooling value from the target subcooling value. Subcooling Deviation = Actual Subcooling - Target Subcooling.
In order to allow for inevitable differences in measurements, the Pass/Fail criteria are different for the Installer than for the HERS Rater. - If the Subcooling Deviation is within the subcooling tolerance allowed by Table RA3.2-1, then the system complies with the subcooling criterion, otherwise the system does not comply.
- For the HVAC installer, if the system does not comply, and if the Actual Subcooling value is greater than the Target Subcooling value, the Installer shall remove refrigerant. If the Actual Subcooling value is less than the Target Subcooling value, the Installer shall add refrigerant. The Installer shall determine whether there are other system faults that may affect the validity of the refrigerant charge verification procedure, and make any needed system repairs or adjustments to clear system faults prior to completion of the refrigerant charge verification procedure. The Installer shall adjust the refrigerant charge and check the measurements as many times as necessary to pass the test. After the final adjustment has been made, the Installer shall allow the system to run 15 minutes before completing the final measurement procedure.
- Calculate Actual Superheat as the suction line temperature minus the evaporator saturation temperature. Actual Superheat = Tsuction, – Tevaporator, sat.
- If possible, determine the Superheat Range specified by the manufacturer.
- In order to allow for inevitable differences in measurements, the Pass/Fail criteria are different for the Installer than for the HERS Rater.
If the superheat is within the tolerance allowed by Table RA3.2-1, then the system complies with the metering device criterion, otherwise the system does not comply.
For the HVAC installer, if the system does not comply remedial actions must be undertaken to ensure the TXV or EXV is operating properly.
This section specifies the weigh-in charging procedure in which the weight of the required refrigerant charge is determined by using the manufacturer's specifications for a standard refrigerant charge weight and taking into account adjustment factors such as deviations in refrigerant line length and diameter. The calculated weight of refrigerant is then installed using a refrigerant scale. RA3.2.3 provides two procedures: Section RA3.2.3.1 shall be used by the HVAC installer when the weigh-in procedure is required by the Standards for compliance. Section RA3.2.3.2 shall be used by the HERS Rater when the Standards specify use of the procedure for compliance, or specify it as an optional procedure for compliance. The weigh-in charging procedure is an acceptable method for demonstrating compliance at any outdoor temperature, however if the weigh-in charging procedure is used, HERS verification of compliance cannot use group sampling.
HVAC installers shall use the weigh-in charging procedure in accordance with the space conditioning system manufacturer’s specifications.
Both the HVAC installer and the HERS Rater shall test the system airflow as specified by Standards Sections 150.1(c)7Aib and 150.2(b)1Fiia as applicable.
Split system air conditioners are shipped from the factory charged with a standard amount of refrigerant as indicated on the nameplate. The manufacturer-supplied refrigerant charge is expected to be the correct amount for the system based on a standard liquid line length and diameter. It is the responsibility of the HVAC installer to ensure that the charge is correct for each air conditioner and to adjust the charge based on liquid line dimensions that deviate from the manufacturer's standard line specification
There shall be two options for compliance using the weigh-in charging procedure:
This option is applicable to a new system or existing system when a new outdoor unit is installed (with factory charge in outdoor unit). The HVAC installer shall weigh in lineset and indoor coil charge adjustment after evacuation of lineset and indoor coil. The documentation shall include the calculated charge adjustment for the lineset.
This option is applicable to all systems. The installer shall weigh in the total system charge after refrigerant recovery and evacuation of the entire system. The total system charge includes the nameplate charge for the outdoor unit and any adjustment for the lineset dimensions and indoor coil in accordance with the manufacturer’s instructions. The documentation shall include the nameplate charge and the calculated lineset adjustment.
Persons who use this procedure to demonstrate compliance with Title 24, Part 6 shall be qualified to perform the following:
- Calculate the correct system charge based on the Manufacturer's standard charge and adjustments to the standard charge based on lineset dimensions and indoor coil.
- Obtain accurate refrigerant charge weight.
Instrumentation for the procedures described in this section shall conform to the following specifications:
An electronic refrigerant scale having an accuracy equal to or better than ±0.5 oz or ± 0.5% of the measured value shall be used.
The accuracy of instrumentation shall be maintained using the following procedures. A sticker with the calibration check date shall be affixed to each instrument calibrated.
Refrigerant scales shall be calibrated according to the manufacturer's recommended procedures. When the manufacturer certifies the calibration for a limited time, the refrigerant scale shall be recalibrated according to the manufacturers required procedure when the calibration period expires.
The weigh-in procedure shall be performed in accordance with all manufacturer specifications to confirm:
- Liquid line filter drier has been installed if required per outdoor condensing unit manufacturer's instructions, and installed with the proper orientation with respect to refrigerant flow, if applicable.
- The system is braised with dry nitrogen in the lines and indoor coil.
- The system is evacuated to 500 microns or less and, when isolated, rises no more than 300 microns over five minutes.
- The lineset correction is calculated based on the length and diameter of the lineset.
- The indoor coil correction to refrigerant weight is used if it is supplied by the manufacturer.
- The amount of charge calculated for the lineset correction (and indoor coil correction if available) is added or removed, or the total charge based on the lineset, indoor coil, and standard label charge is installed.
The HVAC Installer shall certify on the Certificate of Installation that the manufacturer's specifications for these procedures have been met.
When the Standards indicate this procedure is required, or is an option for compliance, the HERS Rater shall coordinate with the HVAC Installer to observe the weigh-in charging procedure.
HERS Rater shall observe and confirm:
- The system is evacuated to 500 microns or less and, when isolated, rises no more than 300 microns over five minutes.
- The lineset correction is calculated based on the length and diameter of the lineset, including the liquid line filter drier if required per outdoor condensing unit manufacturer instructions.
- The indoor coil correction to refrigerant weight is used if it is supplied by the manufacturer.
- The installer adds or removes the amount of charge calculated for the lineset correction or installs the total charge based on lineset, indoor coil, and standard label charge.
- | 50 | 51 | 52 | 53 | 54 | 55 | 56 | 57 | 58 | 59 | 60 | 61 | 62 | 63 | 64 | 65 | 66 | 67 | 68 | 69 | 70 | 71 | 72 | 73 | 74 | 75 | 76 | |
Condenser Air Dry-Bulb Temperature (°F) (T condenser, db ) | 55 | 8.8 | 10.1 | 11.5 | 12.8 | 14.2 | 15.6 | 17.1 | 18.5 | 20.0 | 21.5 | 23.1 | 24.6 | 26.2 | 27.8 | 29.4 | 31.0 | 32.4 | 33.8 | 35.1 | 36.4 | 37.7 | 39.0 | 40.2 | 41.5 | 42.7 | 43.9 | 45.0 |
56 | 8.6 | 9.9 | 11.2 | 12.6 | 14.0 | 15.4 | 16.8 | 18.2 | 19.7 | 21.2 | 22.7 | 24.2 | 25.7 | 27.3 | 28.9 | 30.5 | 31.8 | 33.2 | 34.6 | 35.9 | 37.2 | 38.5 | 39.7 | 41.0 | 42.2 | 43.4 | 44.6 | |
57 | 8.3 | 9.6 | 11.0 | 12.3 | 13.7 | 15.1 | 16.5 | 17.9 | 19.4 | 20.8 | 22.3 | 23.8 | 25.3 | 26.8 | 28.3 | 29.9 | 31.3 | 32.6 | 34.0 | 35.3 | 36.7 | 38.0 | 39.2 | 40.5 | 41.7 | 43.0 | 44.2 | |
58 | 7.9 | 9.3 | 10.6 | 12.0 | 13.4 | 14.8 | 16.2 | 17.6 | 19.0 | 20.4 | 21.9 | 23.3 | 24.8 | 26.3 | 27.8 | 29.3 | 30.7 | 32.1 | 33.5 | 34.8 | 36.1 | 37.5 | 38.7 | 40.0 | 41.3 | 42.5 | 43.7 | |
59 | 7.5 | 8.9 | 10.2 | 11.6 | 13.0 | 14.4 | 15.8 | 17.2 | 18.6 | 20.0 | 21.4 | 22.9 | 24.3 | 25.7 | 27.2 | 28.7 | 30.1 | 31.5 | 32.9 | 34.3 | 35.6 | 36.9 | 38.3 | 39.5 | 40.8 | 42.1 | 43.3 | |
60 | 7.0 | 8.4 | 9.8 | 11.2 | 12.6 | 14.0 | 15.4 | 16.8 | 18.2 | 19.6 | 21.0 | 22.4 | 23.8 | 25.2 | 26.6 | 28.1 | 29.6 | 31.0 | 32.4 | 33.7 | 35.1 | 36.4 | 37.8 | 39.1 | 40.4 | 41.6 | 42.9 | |
61 | 6.5 | 7.9 | 9.3 | 10.7 | 12.1 | 13.5 | 14.9 | 16.3 | 17.7 | 19.1 | 20.5 | 21.9 | 23.3 | 24.7 | 26.1 | 27.5 | 29.0 | 30.4 | 31.8 | 33.2 | 34.6 | 35.9 | 37.3 | 38.6 | 39.9 | 41.2 | 42.4 | |
62 | 6.0 | 7.4 | 8.8 | 10.2 | 11.7 | 13.1 | 14.5 | 15.9 | 17.3 | 18.7 | 20.1 | 21.4 | 22.8 | 24.2 | 25.5 | 27.0 | 28.4 | 29.9 | 31.3 | 32.7 | 34.1 | 35.4 | 36.8 | 38.1 | 39.4 | 40.7 | 42.0 | |
63 | 5.3 | 6.8 | 8.3 | 9.7 | 11.1 | 12.6 | 14.0 | 15.4 | 16.8 | 18.2 | 19.6 | 20.9 | 22.3 | 23.6 | 25.0 | 26.4 | 27.8 | 29.3 | 30.7 | 32.2 | 33.6 | 34.9 | 36.3 | 37.7 | 39.0 | 40.3 | 41.6 | |
64 | - | 6.1 | 7.6 | 9.1 | 10.6 | 12.0 | 13.5 | 14.9 | 16.3 | 17.7 | 19.0 | 20.4 | 21.7 | 23.1 | 24.4 | 25.8 | 27.3 | 28.7 | 30.2 | 31.6 | 33.0 | 34.4 | 35.8 | 37.2 | 38.5 | 39.9 | 41.2 | |
65 | - | 5.4 | 7.0 | 8.5 | 10.0 | 11.5 | 12.9 | 14.3 | 15.8 | 17.1 | 18.5 | 19.9 | 21.2 | 22.5 | 23.8 | 25.2 | 26.7 | 28.2 | 29.7 | 31.1 | 32.5 | 33.9 | 35.3 | 36.7 | 38.1 | 39.4 | 40.8 | |
66 | - | 6.3 | 7.8 | 9.3 | 10.8 | 12.3 | 13.8 | 15.2 | 16.6 | 18.0 | 19.3 | 20.7 | 22.0 | 23.2 | 24.6 | 26.1 | 27.6 | 29.1 | 30.6 | 32.0 | 33.4 | 34.9 | 36.3 | 37.6 | 39.0 | 40.4 | ||
67 | - | - | 5.5 | 7.1 | 8.7 | 10.2 | 11.7 | 13.2 | 14.6 | 16.0 | 17.4 | 18.8 | 20.1 | 21.4 | 22.7 | 24.1 | 25.6 | 27.1 | 28.6 | 30.1 | 31.5 | 33.0 | 34.4 | 35.8 | 37.2 | 38.6 | 39.9 | |
68 | - | - | - | 6.3 | 8.0 | 9.5 | 11.1 | 12.6 | 14.0 | 15.5 | 16.8 | 18.2 | 19.5 | 20.8 | 22.1 | 23.5 | 25.0 | 26.5 | 28.0 | 29.5 | 31.0 | 32.5 | 33.9 | 35.3 | 36.8 | 38.1 | 39.5 | |
69 | - | - | - | 5.5 | 7.2 | 8.8 | 10.4 | 11.9 | 13.4 | 14.8 | 16.3 | 17.6 | 19.0 | 20.3 | 21.5 | 22.9 | 24.4 | 26.0 | 27.5 | 29.0 | 30.5 | 32.0 | 33.4 | 34.9 | 36.3 | 37.7 | 39.1 | |
70 | - | - | - | - | 6.4 | 8.1 | 9.7 | 11.2 | 12.7 | 14.2 | 15.7 | 17.0 | 18.4 | 19.7 | 20.9 | 22.3 | 23.9 | 25.4 | 27.0 | 28.5 | 30.0 | 31.5 | 33.0 | 34.4 | 35.9 | 37.3 | 38.7 | |
71 | - | - | - | - | 5.6 | 7.3 | 8.9 | 10.5 | 12.1 | 13.6 | 15.0 | 16.4 | 17.8 | 19.1 | 20.3 | 21.7 | 23.3 | 24.9 | 26.4 | 28.0 | 29.5 | 31.0 | 32.5 | 34.0 | 35.4 | 36.9 | 38.3 | |
72 | - | - | - | - | - | 6.4 | 8.1 | 9.8 | 11.4 | 12.9 | 14.4 | 15.8 | 17.2 | 18.5 | 19.7 | 21.2 | 22.8 | 24.3 | 25.9 | 27.4 | 29.0 | 30.5 | 32.0 | 33.5 | 35.0 | 36.5 | 37.9 | |
73 | - | - | - | - | - | 5.6 | 7.3 | 9.0 | 10.7 | 12.2 | 13.7 | 15.2 | 16.6 | 17.9 | 19.2 | 20.6 | 22.2 | 23.8 | 25.4 | 26.9 | 28.5 | 30.0 | 31.5 | 33.1 | 34.6 | 36.0 | 37.5 | |
74 | - | - | - | - | - | - | 6.5 | 8.2 | 9.9 | 11.5 | 13.1 | 14.5 | 15.9 | 17.3 | 18.6 | 20.0 | 21.6 | 23.2 | 24.8 | 26.4 | 28.0 | 29.5 | 31.1 | 32.6 | 34.1 | 35.6 | 37.1 | |
75 | - | - | - | - | - | - | 5.6 | 7.4 | 9.2 | 10.8 | 12.4 | 13.9 | 15.3 | 16.7 | 18.0 | 19.4 | 21.1 | 22.7 | 24.3 | 25.9 | 27.5 | 29.1 | 30.6 | 32.2 | 33.7 | 35.2 | 36.7 | |
76 | - | - | - | - | - | - | - | 6.6 | 8.4 | 10.1 | 11.7 | 13.2 | 14.7 | 16.1 | 17.4 | 18.9 | 20.5 | 22.1 | 23.8 | 25.4 | 27.0 | 28.6 | 30.1 | 31.7 | 33.3 | 34.8 | 36.3 | |
77 | - | - | - | - | - | - | - | 5.7 | 7.5 | 9.3 | 11.0 | 12.5 | 14.0 | 15.4 | 16.8 | 18.3 | 20.0 | 21.6 | 23.2 | 24.9 | 26.5 | 28.1 | 29.7 | 31.3 | 32.8 | 34.4 | 36.0 | |
78 | - | - | - | - | - | - | - | - | 6.7 | 8.5 | 10.2 | 11.8 | 13.4 | 14.8 | 16.2 | 17.7 | 19.4 | 21.1 | 22.7 | 24.4 | 26.0 | 27.6 | 29.2 | 30.8 | 32.4 | 34.0 | 35.6 | |
79 | - | - | - | - | - | - | - | - | 5.9 | 7.7 | 9.5 | 11.1 | 12.7 | 14.2 | 15.6 | 17.1 | 18.8 | 20.5 | 22.2 | 23.8 | 25.5 | 27.1 | 28.8 | 30.4 | 32.0 | 33.6 | 35.2 | |
80 | - | - | - | - | - | - | - | - | - | 6.9 | 8.7 | 10.4 | 12.0 | 13.5 | 15.0 | 16.6 | 18.3 | 20.0 | 21.7 | 23.3 | 25.0 | 26.7 | 28.3 | 29.9 | 31.6 | 33.2 | 34.8 | |
81 | - | - | - | - | - | - | - | - | - | 6.0 | 7.9 | 9.7 | 11.3 | 12.9 | 14.3 | 16.0 | 17.7 | 19.4 | 21.1 | 22.8 | 24.5 | 26.2 | 27.9 | 29.5 | 31.2 | 32.8 | 34.4 | |
82 | - | - | - | - | - | - | - | - | - | 5.2 | 7.1 | 8.9 | 10.6 | 12.2 | 13.7 | 15.4 | 17.2 | 18.9 | 20.6 | 22.3 | 24.0 | 25.7 | 27.4 | 29.1 | 30.7 | 32.4 | 34.0 | |
83 | - | - | - | - | - | - | - | - | - | - | 6.3 | 8.2 | 9.9 | 11.6 | 13.1 | 14.9 | 16.6 | 18.4 | 20.1 | 21.8 | 23.5 | 25.2 | 26.9 | 28.6 | 30.3 | 32.0 | 33.7 | |
84 | - | - | - | - | - | - | - | - | - | - | 5.5 | 7.4 | 9.2 | 10.9 | 12.5 | 14.3 | 16.1 | 17.8 | 19.6 | 21.3 | 23.0 | 24.8 | 26.5 | 28.2 | 29.9 | 31.6 | 33.3 | |
85 | - | - | - | - | - | - | - | - | - | - | - | 6.6 | 8.5 | 10.3 | 11.9 | 13.7 | 15.5 | 17.3 | 19.0 | 20.8 | 22.6 | 24.3 | 26.0 | 27.8 | 29.5 | 31.2 | 32.9 | |
86 | - | - | - | - | - | - | - | - | - | - | - | 5.8 | 7.8 | 9.6 | 11.3 | 13.2 | 15.0 | 16.7 | 18.5 | 20.3 | 22.1 | 23.8 | 25.6 | 27.3 | 29.1 | 30.8 | 32.6 | |
87 | - | - | - | - | - | - | - | - | - | - | - | 5.0 | 7.0 | 8.9 | 10.6 | 12.6 | 14.4 | 16.2 | 18.0 | 19.8 | 21.6 | 23.4 | 25.1 | 26.9 | 28.7 | 30.4 | 32.2 | |
88 | - | - | - | - | - | - | - | - | - | - | - | - | 6.3 | 8.2 | 10.0 | 12.0 | 13.9 | 15.7 | 17.5 | 19.3 | 21.1 | 22.9 | 24.7 | 26.5 | 28.3 | 30.1 | 31.8 | |
89 | - | - | - | - | - | - | - | - | - | - | - | - | 5.5 | 7.5 | 9.4 | 11.5 | 13.3 | 15.1 | 17.0 | 18.8 | 20.6 | 22.4 | 24.3 | 26.1 | 27.9 | 29.7 | 31.5 |
Return Air Wet-Bulb Temperature (°F)
(T return, wb)
Return Air Wet-Bulb Temperature (°F) (T return, wb) | ||||||||||||||||||||||||||||
50 | 51 | 52 | 53 | 54 | 55 | 56 | 57 | 58 | 59 | 60 | 61 | 62 | 63 | 64 | 65 | 66 | 67 | 68 | 69 | 70 | 71 | 72 | 73 | 74 | 75 | 76 | ||
Condenser Air Dry-Bulb Temperature (°F) (T condenser, db) | 90 | - | - | - | - | - | - | - | - | - | - | - | - | - | 6.8 | 8.8 | 10.9 | 12.8 | 14.6 | 16.5 | 18.3 | 20.1 | 22.0 | 23.8 | 25.6 | 27.5 | 29.3 | 31.1 |
91 | - | - | - | - | - | - | - | - | - | - | - | - | - | 6.1 | 8.1 | 10.3 | 12.2 | 14.1 | 15.9 | 17.8 | 19.7 | 21.5 | 23.4 | 25.2 | 27.1 | 28.9 | 30.8 | |
92 | - | - | - | - | - | - | - | - | - | - | - | - | - | 5.4 | 7.5 | 9.8 | 11.7 | 13.5 | 15.4 | 17.3 | 19.2 | 21.1 | 22.9 | 24.8 | 26.7 | 28.5 | 30.4 | |
93 | - | - | - | - | - | - | - | - | - | - | - | - | - | - | 6.8 | 9.2 | 11.1 | 13.0 | 14.9 | 16.8 | 18.7 | 20.6 | 22.5 | 24.4 | 26.3 | 28.2 | 30.1 | |
94 | - | - | - | - | - | - | - | - | - | - | - | - | - | - | 6.2 | 8.7 | 10.6 | 12.5 | 14.4 | 16.3 | 18.2 | 20.2 | 22.1 | 24.0 | 25.9 | 27.8 | 29.7 | |
95 | - | - | - | - | - | - | - | - | - | - | - | - | - | - | 5.6 | 8.1 | 10.0 | 12.0 | 13.9 | 15.8 | 17.8 | 19.7 | 21.6 | 23.6 | 25.5 | 27.4 | 29.4 | |
96 | - | - | - | - | - | - | - | - | - | - | - | - | - | - | - | 7.5 | 9.5 | 11.4 | 13.4 | 15.3 | 17.3 | 19.2 | 21.2 | 23.2 | 25.1 | 27.1 | 29.0 | |
97 | - | - | - | - | - | - | - | - | - | - | - | - | - | - | - | 7.0 | 8.9 | 10.9 | 12.9 | 14.9 | 16.8 | 18.8 | 20.8 | 22.7 | 24.7 | 26.7 | 28.7 | |
98 | - | - | - | - | - | - | - | - | - | - | - | - | - | - | - | 6.4 | 8.4 | 10.4 | 12.4 | 14.4 | 16.4 | 18.3 | 20.3 | 22.3 | 24.3 | 26.3 | 28.3 | |
99 | - | - | - | - | - | - | - | - | - | - | - | - | - | - | - | 5.8 | 7.9 | 9.9 | 11.9 | 13.9 | 15.9 | 17.9 | 19.9 | 21.9 | 24.0 | 26.0 | 28.0 | |
100 | - | - | - | - | - | - | - | - | - | - | - | - | - | - | - | 5.3 | 7.3 | 9.3 | 11.4 | 13.4 | 15.4 | 17.5 | 19.5 | 21.5 | 23.6 | 25.6 | 27.7 | |
101 | - | - | - | - | - | - | - | - | - | - | - | - | - | - | - | - | 6.8 | 8.8 | 10.9 | 12.9 | 15.0 | 17.0 | 19.1 | 21.1 | 23.2 | 25.3 | 27.3 | |
102 | - | - | - | - | - | - | - | - | - | - | - | - | - | - | - | - | 6.2 | 8.3 | 10.4 | 12.4 | 14.5 | 16.6 | 18.6 | 20.7 | 22.8 | 24.9 | 27.0 | |
103 | - | - | - | - | - | - | - | - | - | - | - | - | - | - | - | - | 5.7 | 7.8 | 9.9 | 11.9 | 14.0 | 16.1 | 18.2 | 20.3 | 22.4 | 24.5 | 26.7 | |
104 | - | - | - | - | - | - | - | - | - | - | - | - | - | - | - | - | 5.2 | 7.2 | 9.3 | 11.5 | 13.6 | 15.7 | 17.8 | 19.9 | 22.1 | 24.2 | 26.3 |
Return Air Wet-Bulb Temperature (°F)
(T return, wb)
Return Air Wet-Bulb Temperature (°F) (T return, wb) | |||||||||||||||||||||||||||||
50 | 51 | 52 | 53 | 54 | 55 | 56 | 57 | 58 | 59 | 60 | 61 | 62 | 63 | 64 | 65 | 66 | 67 | 68 | 69 | 70 | 71 | 72 | 73 | 74 | 75 | 76 | |||
Condenser Air Dry-Bulb Temperature (°F) (T condenser, db) | 90 | - | - | - | - | - | - | - | - | - | - | - | - | - | 6.8 | 8.8 | 10.9 | 12.8 | 14.6 | 16.5 | 18.3 | 20.1 | 22.0 | 23.8 | 25.6 | 27.5 | 29.3 | 31.1 | |
91 | - | - | - | - | - | - | - | - | - | - | - | - | - | 6.1 | 8.1 | 10.3 | 12.2 | 14.1 | 15.9 | 17.8 | 19.7 | 21.5 | 23.4 | 25.2 | 27.1 | 28.9 | 30.8 | ||
92 | - | - | - | - | - | - | - | - | - | - | - | - | - | 5.4 | 7.5 | 9.8 | 11.7 | 13.5 | 15.4 | 17.3 | 19.2 | 21.1 | 22.9 | 24.8 | 26.7 | 28.5 | 30.4 | ||
93 | - | - | - | - | - | - | - | - | - | - | - | - | - | - | 6.8 | 9.2 | 11.1 | 13.0 | 14.9 | 16.8 | 18.7 | 20.6 | 22.5 | 24.4 | 26.3 | 28.2 | 30.1 | ||
94 | - | - | - | - | - | - | - | - | - | - | - | - | - | - | 6.2 | 8.7 | 10.6 | 12.5 | 14.4 | 16.3 | 18.2 | 20.2 | 22.1 | 24.0 | 25.9 | 27.8 | 29.7 | ||
95 | - | - | - | - | - | - | - | - | - | - | - | - | - | - | 5.6 | 8.1 | 10.0 | 12.0 | 13.9 | 15.8 | 17.8 | 19.7 | 21.6 | 23.6 | 25.5 | 27.4 | 29.4 | ||
96 | - | - | - | - | - | - | - | - | - | - | - | - | - | - | - | 7.5 | 9.5 | 11.4 | 13.4 | 15.3 | 17.3 | 19.2 | 21.2 | 23.2 | 25.1 | 27.1 | 29.0 | ||
97 | - | - | - | - | - | - | - | - | - | - | - | - | - | - | - | 7.0 | 8.9 | 10.9 | 12.9 | 14.9 | 16.8 | 18.8 | 20.8 | 22.7 | 24.7 | 26.7 | 28.7 | ||
98 | - | - | - | - | - | - | - | - | - | - | - | - | - | - | - | 6.4 | 8.4 | 10.4 | 12.4 | 14.4 | 16.4 | 18.3 | 20.3 | 22.3 | 24.3 | 26.3 | 28.3 | ||
99 | - | - | - | - | - | - | - | - | - | - | - | - | - | - | - | 5.8 | 7.9 | 9.9 | 11.9 | 13.9 | 15.9 | 17.9 | 19.9 | 21.9 | 24.0 | 26.0 | 28.0 | ||
100 | - | - | - | - | - | - | - | - | - | - | - | - | - | - | - | 5.3 | 7.3 | 9.3 | 11.4 | 13.4 | 15.4 | 17.5 | 19.5 | 21.5 | 23.6 | 25.6 | 27.7 | ||
101 | - | - | - | - | - | - | - | - | - | - | - | - | - | - | - | - | 6.8 | 8.8 | 10.9 | 12.9 | 15.0 | 17.0 | 19.1 | 21.1 | 23.2 | 25.3 | 27.3 | ||
102 | - | - | - | - | - | - | - | - | - | - | - | - | - | - | - | - | 6.2 | 8.3 | 10.4 | 12.4 | 14.5 | 16.6 | 18.6 | 20.7 | 22.8 | 24.9 | 27.0 | ||
103 | - | - | - | - | - | - | - | - | - | - | - | - | - | - | - | - | 5.7 | 7.8 | 9.9 | 11.9 | 14.0 | 16.1 | 18.2 | 20.3 | 22.4 | 24.5 | 26.7 | ||
104 | - | - | - | - | - | - | - | - | - | - | - | - | - | - | - | - | 5.2 | 7.2 | 9.3 | 11.5 | 13.6 | 15.7 | 17.8 | 19.9 | 22.1 | 24.2 | 26.3 | ||
105 | - | - | - | - | - | - | - | - | - | - | - | - | - | - | - | - | - | 6.7 | 8.8 | 11.0 | 13.1 | 15.2 | 17.4 | 19.5 | 21.7 | 23.8 | 26.0 | ||
106 | - | - | - | - | - | - | - | - | - | - | - | - | - | - | - | - | - | 6.2 | 8.3 | 10.5 | 12.6 | 14.8 | 17.0 | 19.1 | 21.3 | 23.5 | 25.7 | ||
107 | - | - | - | - | - | - | - | - | - | - | - | - | - | - | - | - | - | 5.7 | 7.9 | 10.0 | 12.2 | 14.4 | 16.6 | 18.7 | 21.0 | 23.2 | 25.4 | ||
108 | - | - | - | - | - | - | - | - | - | - | - | - | - | - | - | - | - | 5.2 | 7.4 | 9.5 | 11.7 | 13.9 | 16.1 | 18.4 | 20.6 | 22.8 | 25.1 | ||
109 | - | - | - | - | - | - | - | - | - | - | - | - | - | - | - | - | - | - | 6.9 | 9.1 | 11.3 | 13.5 | 15.7 | 18.0 | 20.2 | 22.5 | 24.7 | ||
110 | - | - | - | - | - | - | - | - | - | - | - | - | - | - | - | - | - | - | 6.4 | 8.6 | 10.8 | 13.1 | 15.3 | 17.6 | 19.9 | 22.1 | 24.4 | ||
111 | - | - | - | - | - | - | - | - | - | - | - | - | - | - | - | - | - | - | 5.9 | 8.1 | 10.4 | 12.6 | 14.9 | 17.2 | 19.5 | 21.8 | 24.1 | ||
112 | - | - | - | - | - | - | - | - | - | - | - | - | - | - | - | - | - | - | 5.4 | 7.6 | 9.9 | 12.2 | 14.5 | 16.8 | 19.1 | 21.5 | 23.8 | ||
113 | - | - | - | - | - | - | - | - | - | - | - | - | - | - | - | - | - | - | - | 7.2 | 9.5 | 11.8 | 14.1 | 16.4 | 18.8 | 21.1 | 23.5 | ||
114 | - | - | - | - | - | - | - | - | - | - | - | - | - | - | - | - | - | - | - | 6.7 | 9.0 | 11.4 | 13.7 | 16.1 | 18.4 | 20.8 | 23.2 | ||
115 | - | - | - | - | - | - | - | - | - | - | - | - | - | - | - | - | - | - | - | 6.2 | 8.6 | 10.9 | 13.3 | 15.7 | 18.1 | 20.5 | 22.9 |