All of the ventilation and indoor air quality requirements are mandatory measures. Some measures require acceptance testing, which is addressed in Chapter 13.
Within a building, all occupied space that is normally used by humans must be continuously ventilated during occupied hours with outdoor air, using either natural or mechanical ventilation as specified in §120.1(c). Ventilation requirements for healthcare facilities should conform to the requirements in Chapter 4 of the California Mechanical Code.
“Spaces normally used by humans” refers to spaces where people can be reasonably expected to remain for an extended period of time. Spaces where occupancy will be brief and intermittent that do not have any unusual sources of air contaminants do not need to be directly ventilated. For example:
- A closet, provided it is not normally occupied
- A storeroom that is only infrequently or briefly occupied. However, a storeroom that can be expected to be occupied for extended periods for clean-up or inventory must be ventilated, preferably with systems controlled by a local switch so that the ventilation system operates only when the space is occupied.
“Continuously ventilated during occupied hours” implies that minimum ventilation must be provided throughout the entire occupied period. Meaning variable air volume (VAV) systems must provide the code-required ventilation over the full range of operating supply airflow. Some means of dynamically controlling the minimum ventilation air must be provided.
Occupied spaces may be subjected to poor indoor air quality if poor quality outdoor air is brought in without first being cleaned. Particles less than 2.5 µm are referred to as “fine” particles, and because of their small size, can lodge deeply into the lungs. There is a strong correlation between exposure to fine particles and premature mortality. Other effects of particulate matter exposure include respiratory and cardiovascular disease. Because of these adverse health effects, advances in filtration technology and market availability, removal of fine particulate contaminants by use of filtration is reasonable and achievable. The Energy Code requires that filters have a particle removal efficiency equal to or greater than the minimum efficiency reporting value (MERV) 13 when tested in accordance with ASHRAE Standard 52.2, or a particle size efficiency rating equal to or greater than 50 percent in the 0.3-1.0 µm and 85 percent in the 1.0-3.0 µm range when tested in accordance with AHRI Standard 680.
The following system types are required to provide air filtration:
- Mechanical space conditioning (heating or cooling) systems that utilize forced air ducts greater than 10 feet in length to supply air to an occupied space. The total is determined by summing the lengths of all the supply and return ducts for the force air system.
- Mechanical supply-only ventilation systems that provide outside air to an occupied space.
- The supply side of mechanical balanced ventilation systems, including heat recovery ventilator and energy recovery ventilators that provide outside air to an occupied space.
Space conditioning systems and ventilation systems in nonresidential and hotel/motel occupancies may use either of the two following compliance approaches:
- Install a filter grille or accessible filter rack sized by the system designer that accommodates a minimum 2-inch depth filter and install the appropriate filter.
- Install a filter grille or accessible filter rack that accommodates a minimum 1-inch depth filter and install the appropriate filter. The filter/grille must be sized for a velocity of less than or equal to 150 ft per minute. The installed filter must be labeled to indicate the pressure drop across the filter at the design airflow rate for that return is less than or equal to 0.1-inch w.c. (25 PA). Use the following method to calculate the 1 inch per min. This yields a value for the face area in sq ft. Since air filters are sold using nominal sizes in terms of inches, convert the face area to sq in by multiplying the face area (sq ft) by a conversion factor of 144 sq inch/sq ft. Refer also to Equation 4-7 above.
Field verification and diagnostic testing of system airflow in accordance with the procedures in NA1 (HERS verification) is not required for nonresidential and hotel/motel occupancies.
Air filter pressure drop can be reduced by increasing the amount of air filter media surface area available to the system’s airflow. Increased media surface area can be accomplished by adjusting one, two, or three of the following factors:
All filters must be accessible to facilitate replacement.
An example of an air filter grille sticker showing the design airflow and pressure drop for the filter grille/rack is shown in Figure 4-2.
Figure 4-2: Example of Installer's Filter Grille Sticker
Air Filter Performance Requirement | Air Filter Performance Requirement | Maintenance Instructions |
Airflow Rate (CFM) Must be greater than or equal to the value shown | Initial Resistance (IWC) Must be less than or equal to the value shown | Use only replacement filters that are rated to simultaneously meet both of the performance requirements specified on this sticker. |
750 | 0.1 | Use only replacement filters that are rated to simultaneously meet both of the performance requirements specified on this sticker. |
Source: California Energy Commission
Figure 4-3: Example Manufacturer's Filter Label Example

Source: California Energy Commission
In order for a filter to meet the system's specifications for airflow and pressure drop, it must be rated by the manufacturer to simultaneously provide more than the specified airflow at less than the specified pressure drop. It is unlikely that a filter will be available that is rated to have the exact airflow and pressure drop ratings specified, so filters should be selected that are rated to have less than the specified pressure drop at the specified airflow rate, otherwise select filters that are rated to have greater than the specified airflow rate at the specified pressure drop. See Figure 4-4 for an example of an installer's filter grille sticker that provides an air filter rating specification for minimum airflow of 750 cfm at maximum pressure drop 0.1-inch w.c.
Air filter manufacturers may make supplementary product information available to consumers to assist with selecting the proper replacement filters. This product information may provide more detailed information about their filter model airflow and pressure drop performance - details such as airflow and pressure drop values that are intermediate values that lie between the values shown on their product label. The information may be published in tables, graphs, or presented in software applications available on the internet or at the point of sale.
Figure 4-4 below shows a graphical representation of the initial resistance (pressure drop) and airflow rate ordered pairs given on the example air filter manufacturer's label shown in Figure 4-3 above. The graph in Figure 4-4 makes it possible to visually determine the airflow rate at 0.1-inch w.c. pressure drop for which the values are not shown on the manufacturer's filter label.
If there is no supplementary manufacturer information available and it is necessary to determine a filter model's performance at an airflow rate or pressure drop, linear interpolation may be used. Example formulas for are shown below.
This method may be used to determine an unknown pressure drop corresponding to a known airflow rate by use of Equation 4-8a, or it may also be used to determine an unknown airflow rate corresponding to a known pressure drop by use of Equation 4-8b.
p = p1 + [(f-f1) ÷ (f2-f1)] x (p2 – p1)
where:
f = a known flow value between f1 and f2
p = the unknown pressure drop value corresponding to f
p1 and p2 = known values that are less than and greater than p respectively
f1 and f2 are the known values corresponding to p1 and p2
f = f1 + [(p-p1) ÷ (p2-p1)] x (f2 – f1)
where:
p = a known pressure drop value between p1 and p2
f = the unknown flow value corresponding to p
f1 and f2 = known values that are less than and greater than f respectively
p1 and p2 are the known values corresponding to f1 and f2
See Example 4-7 for sample calculations that determine the filter's rated airflow corresponding to a known pressure drop specification (0.1-inch w.c.).
Figure 4-4: Plot of Pressure Drop vs. Airflow for a 20" X 30" X 1" Depth Air Filter
From Manufacturer Label Information
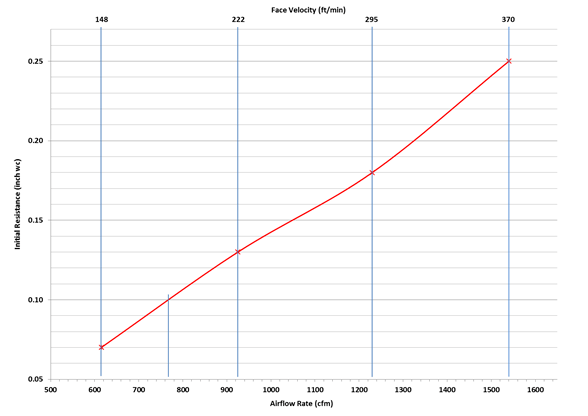
Source: California Energy Commission
Example 4-7: Filter Selection Using Linear Interpolation
Question
Does the air filter label in Figure 4-3 indicate the filter would meet the airflow (750 cfm) and pressure drop (0.1-inch w.c.) requirements shown on the installer filter grille sticker in figure 4-2? How the airflow rate at 0.1-inch w.c. for the manufacturer's filter label shown in Figure 4-3 be determined?
Answer
The filter must be rated to provide greater than 750 cfm at the specified 0.1-inch w.c. pressure drop, or equivalently: the filter must be rated to provide a pressure drop less than 0.1-inch w.c. at the specified 750 cfm.
Referring to equation 4-8b, calculate the unknown value "f" in cfm that corresponds to the known value "p" of 0.1-inch w.c.
Referring to Figure 4-4: p1=0.7, p2=0.13, f1=615, f2=925, and applying Equation 4-8b:
615 + [(0.1-0.07) ÷ (0.13-0.07)] x (925-615) yields 770 cfm
Therefore, since the filter is rated for greater than 750 cfm at 0.1-inch w.c., the filter complies.
Example 4-8: Filter Sizing
Question
A 1,200-cfm furnace is being installed in a new dwelling unit. It has a 20" x 20" x 1” inch filter rack furnished with a 1-inch depth filter installed in the unit. Is this filter in compliance?
Answer
The nominal face area of the filter rack is 20 inches by 20 inches to equal 400 sq in and since it is a 1-inch filter, the face area may not be less than 1200 (cfm)/150 (ft/min) x144 (in2 / ft2) = 1,152 sq in. Therefore, this filter installation does not comply.
Example 4-9
Question
For the same 1200 cfm furnace, what other options are there?
Answer
The filter will be in compliance if it has a depth of 2” or more and is properly sized by the system designer such that the duct system as a whole will be capable of meeting the HERS verification for fan efficacy specified in Section 150.0(m)13.
Otherwise, the required total system filter face area of 1,152 sq inches must be met using multiple remote wall or ceiling filter grilles for which the sum of the face areas is equal to or greater than 1152 sq inches, and the filters must be rated for pressure drop of 0.1 inch w.c. or less at the design airflow rates of each filter grille.
For any filter, the pressure drop, efficiency, and length of time the filter can remain in operation without becoming fully loaded with dust can all be improved by using filters that are deeper than 1 inch. As the depth of the filter is increased, the pressure drop across the filter at the same face area will be greatly reduced.
Example 4-10
Question
A ductless split system is being installed in a home. Must a designated MERV 13 filter be used?
Answer
No, the filtration requirements do not apply unless there is at least 10 feet of duct is attached to the unit.
Example 4-11
Question
If a customer has allergies and wants a MERV 16 or better filter. Is this in compliance?
Answer
Yes, a filtration greater than MERV 13 meets (exceeds) the minimum particle removal efficiency requirement, thus may be used provided all other applicable requirements in 120.1(b)1 are complied with.
The 2019 Energy Code changed the way naturally ventilated spaces are calculated by adopting ASHRAE 62.1. Under these new requirements, naturally ventilated spaces or portions of spaces must be permanently open to and within certain distances of operable wall openings to the outdoors. The space being ventilated, the size of the operable opening and the control of the opening are all considered under these new requirements. Naturally ventilated spaces must also include a mechanical ventilation system that complies with §120.1(c)3 as described in Section 4.3.3., except when the opening to the outdoors is permanently open or has controls that prevent the opening from being closed during periods of expected occupancy. This requirement for mechanical ventilation back-up to a naturally ventilated space protects the occupants from times or events where the outdoor air is not adequate for ventilation and does not rely on an individual to open the opening.
The space to be naturally ventilated is determined based on the configuration of the walls (cross-ventilation, single-sided or adjacent walls) and the ceiling height. For spaces with an operable opening on only one side of the space, only the floor area within two times the ceiling height from the opening is permitted to be naturally ventilated. For spaces with operable openings on two opposite sides of the space, only the floor areas within five times the ceiling height from the openings are permitted to be naturally ventilated. For spaces with operable openings on two adjacent sides of the space (two sides of a corner), only the floor areas along lines connecting the two openings that are within five times the ceiling height meet the requirement. Floor areas not along these lines connecting the windows must meet the one side or two opposite side opening calculation to be permitted to be naturally ventilated. The ceiling height for all of these cases is the minimum ceiling height, except for when the ceiling is sloped upwards from the opening. In that case, the ceiling height is calculated as the average within 20 feet of the opening.
Spaces or portions of space being naturally ventilated must be permanently open to operable walls openings directly to the outdoors. The minimum openable area is required to be 4 percent of the net occupiable floor area being naturally ventilated. Where openings are covered with louvers or otherwise obstructed, the openable area must be based on the free unobstructed area through the opening. Where interior spaces without direct openings to the outdoors are ventilated through adjoining rooms, the opening between rooms must be permanently unobstructed and have a free area of not less than 8 percent of the area of the interior room nor less than 25 sq. ft.
The means to open required operable openings must be readily accessible to building occupants whenever the space is occupied. The operable opening must be monitored to coordinate the operation of the operable opening and the mechanical ventilation system. This is achieved through window contact switches or another type of relay switch that interlocks the operable opening with the mechanical ventilation system. [§140.4(n)]
Mechanical outdoor ventilation must be provided for all spaces normally occupied. The Energy Code requires that a mechanical ventilation system provide outdoor air equal to or exceeding the ventilation rates required for each of the spaces that it serves. At the space, the required ventilation can be provided either directly through supply air or indirectly through transfer of air from the plenum or an adjacent space (see 4.3.6 for updates to transfer air classification). The required minimum ventilation airflow at the space can be provided by an equal quantity of supply or transfer air. At the air-handling unit, the minimum outside air must be the sum of the ventilation requirements of each of the spaces that it serves. The designer may specify higher outside air ventilation rates based on the owner’s preference or specific ventilation needs associated with the space. However, specifying more ventilation air than the minimum allowable ventilation rates increases energy consumption and electrical peak demand and increases the costs of operating the HVAC equipment. Thus, the designer should have a compelling reason to specify higher design minimum outside air rates than the calculated minimum outside air requirements.
The minimum outside air (OSA) as measured by acceptance testing, is required to be within 10 percent of the design minimum for both VAV and constant volume units. The design minimum outside air can be no less than the calculated minimum outside air
In summary:
- Ventilation compliance at the space is satisfied by providing supply and/or transfer air.
- Ventilation compliance at the air handling system level is satisfied by providing, at minimum, the outdoor air that represents the sum of the ventilation requirements of all the spaces that it serves.
For each space requiring mechanical ventilation the ventilation rates must be either:
- The conditioned floor area of the space multiplied by the area outdoor air rate (Ra) from Table 4-12. This provides dilution for the building-borne contaminants like off-gassing of paints and carpets, or
- For spaces designed for an expected number of occupants per the Exception to Section 1004.5 of the CBC, or spaces with fixed seating, the outdoor airflow rate to the zone must be the larger of 15 cfm per person, multiplied by the expected number of occupants or the minimum airflow rate allowed for DCV in Table 4-12, multiplied by the zone floor area. For spaces with fixed seating (such as a theater or auditorium), the expected number of occupants is the number of fixed seats or as determined by the California Building Code.
Occupancy Category | Area Outdoor cfm/ Air rate1 Ra cfm/ft2 | Min Air Rate for DCV2 cfm/ft2 | Air Class | Notes | |
Educational Facilities | |||||
Daycare (through age 4) | 0.21 | 0.15 | 2 | ||
Daycare sickroom | 0.15 | 3 | |||
Classrooms (ages 5-8) | 0.38 | 0.15 | 1 | ||
Classrooms (age 9 -18) | 0.38 | 0.15 | 1 | ||
Lecture/postsecondary classroom | 0.38 | 0.15 | 1 | F | |
Lecture hall (fixed seats) | - | 0.15 | 1 | F | |
Art classroom | 0.15 | 2 | |||
Science laboratories | 0.15 | 2 | |||
University/college laboratories | 0.15 | 2 | |||
Wood/metal shop | 0.15 | 2 | |||
Computer lab | 0.15 | 1 | |||
Media center | 0.15 | 1 | A | ||
Music/theater/dance | 1.07 * | 0.15 | 1 | F | |
Multiuse assembly | 0.50 | 0.15 | 1 | F | |
Food and Beverage Service | |||||
Restaurant dining rooms | 0.50 | 0.15 | 2 | ||
Cafeteria/fast-food dining | 0.50 | 0.15 | 2 | ||
Bars, cocktail lounges | 0.50 | 0.20 | 2 | ||
Kitchen (cooking) | 0.15 | 2 | |||
General | |||||
Break rooms | 0.50 | 0.15 | 1 | F | |
Coffee stations | 0.50 | 0.15 | 1 | F | |
Conference/meeting | 0.50 | 0.15 | 1 | F | |
Corridors | 0.15 | 1 | F | ||
Occupiable storage rooms for liquids or gels | 0.15 | 2 | B | ||
Hotels, Motels, Resorts, Dormitories | |||||
Bedroom/living room | 0.15 | 1 | F | ||
Barracks sleeping areas | 0.15 | 1 | F | ||
Laundry rooms, central | 0.15 | 2 | |||
Laundry rooms within dwelling units | 0.15 | 1 | |||
Lobbies/pre-function | 0.50 | 0.15 | 1 | F | |
Multipurpose assembly | 0.50 | 1 | F | ||
Office Buildings | |||||
Breakrooms | 0.50 | 0.15 | 1 | ||
Main entry lobbies | 0.50 | 0.15 | 1 | F | |
Occupiable storage rooms for dry materials | 0.15 | 1 | |||
Office space | 0.15 | 1 | F | ||
Reception areas | 0.15 | 1 | F | ||
Telephone/data entry | 0.15 | 1 | F | ||
Miscellaneous Spaces | |||||
Bank vaults/safe deposit | 0.15 | 2 | F | ||
Banks or bank lobbies | 0.15 | 1 | F | ||
Computer (not printing) | 0.15 | 1 | F | ||
Freezer and refrigerated spaces (<50 o F) | - | 2 | E | ||
General manufacturing (excludes heavy industrial and process using chemicals) | 0.15 | 3 | |||
Pharmacy (prep. Area) | 0.15 | 2 | |||
Photo studios | 0.15 | 1 | |||
Shipping/receiving | 0.15 | 2 | B | ||
Sorting, packing, light assembly | 0.15 | 2 | |||
Telephone closets | 0.15 | 1 | |||
Transportation waiting | 0.50 | 0.15 | 1 | F | |
Warehouses | 0.15 | 2 | B | ||
All others | 0.15 | 2 | |||
Public Assembly Spaces | |||||
Auditorium seating area | 1.07 a | 0.15 | 1 | F | |
Places of religious worship | 1.07 a | 0.15 | 1 | F | |
Courtrooms | 0.19 a | 0.15 | 1 | F | |
Legislative chambers | 0.19 a | 0.15 | 1 | F | |
Libraries (reading rooms and stack areas) | 0.15 | 1 | |||
Lobbies | 0.50 | 0.15 | 1 | F | |
Museums (children’s) | 0.25 | 0.15 | 1 | ||
Museums/galleries | 0.25 | 0.15 | 1 | F | |
Residential | |||||
Common corridors | 0.15 | 1 | F | ||
Retail | |||||
Sales (except as below) | 0.25 | 0.20 | 2 | ||
Mall common areas | 0.25 | 0.15 | 1 | F | |
Barbershop | 0.40 | 2 | |||
Beauty and nail salons | 0.40 | 2 | |||
Pet shops (animal areas) | 0.25 | 0.15 | 2 | ||
Supermarket | 0.25 | 0.20 | 1 | F | |
Coin-operated laundries | 0.30 | 2 | |||
Sports and Entertainment | |||||
Gym, sports arena (play area) | 0.50 | 0.15 | 2 | E | |
Spectator areas | 0.50 | 0.15 | 1 | F | |
Swimming (pool) | 0.15 | 2 | C | ||
Swimming (deck) | 0.50 | 0.15 | 2 | C | |
Disco/dance floors | 1.50 | 0.15 | 2 | F | |
Health club/aerobics room | 0.15 | 2 | |||
Health club/weight rooms | 0.15 | 2 | |||
Bowling alley (seating) | 1.07 | 0.15 | 1 | ||
Gambling casinos | 0.68 | 0.15 | 1 | ||
Game arcades | 0.68 | 0.15 | 1 | ||
Stages, studios | 0.50 | 0.15 | 1 | D,F |
General notes:
1 Ra was determined as being the larger of the area method and the default per person method. The occupant density used in the per person method was assumed to be one half of the maximum occupant load assumed for egress purposes in the California Building Code.
2 If this column specifies a minimum cfm/ft2 then it shall be used to comply with Section 120.1(d)4E.
Specific notes:
A – For high-school and college libraries, the values shown for “Public Assembly Spaces – Libraries” shall be used. B – Rate may not be sufficient where stored materials include those having potentially harmful emissions.
C – Rate does not allow for humidity control. “Deck area” refers to the area surrounding the pool that is capable of being wetted during pool use or when the pool is occupied. Deck area that is not expected to be wetted shall be designated as an occupancy category.
D – Rate does not include special exhaust for stage effects such as dry ice vapors and smoke.
E – Where combustion equipment is intended to be used on the playing surface or in the space, additional dilution ventilation, source control, or both shall be provided.
F – Ventilation air for this occupancy category shall be permitted to be reduced to zero when the space is in occupied-standby mode
Source: California Energy Commission, 2022 Building Energy Efficiency Standards, Table 120.1-A
As previously stated, each ventilation system must provide outdoor ventilation air as follows:
- For a ventilation system serving a single space, the required system outdoor airflow is equal to the design outdoor ventilation rate of the space.
- For a ventilation system serving multiple spaces, the required outdoor air quantity delivered by the system must not be less than the sum of the required outdoor ventilation rate to each space. The Energy Code do not require that each space actually receive its exact calculated outdoor air quantity. Instead, the supply air to any given space may be any combination of recirculated air, outdoor air, or air transferred directly from other spaces, provided:
- The total amount of outdoor air delivered by the ventilation system(s) to all spaces is at least as large as the sum of the space design quantities.
- Each space always receives supply airflow, including recirculated air and/or transfer air, no less than the calculated outdoor ventilation rate.
- When using transfer air, none of the spaces from which air is transferred has any unusual sources of contaminants.
Example 4-9: Ventilation for a Two-Room Building
Question
Consider a building with two spaces, each having an area of 1,000 sq ft. One space is used for general administrative functions, and the other is used as a classroom. It is estimated that the office will contain seven people, and the classroom will contain 50 people (fixed seating). What are the required outdoor ventilation rates?
- For the office area, the design outdoor ventilation air is the larger of:
7 people x 15 cfm/person = 105 cfm; or
1,000 ft2 x 0.15 cfm/ft2 = 150 cfm
For this space, the design ventilation rate is 150 cfm. - For the classroom, the design outdoor ventilation air is the larger of:
50 people x 15 cfm/person = 750 cfm; or
1,000 ft2 x 0.38 cfm/ft2 = 380 cfm
For this space the design ventilation rate is 750 cfm.
Assume the total supply air necessary to satisfy cooling loads is 1,000 cfm for the office and 1,500 cfm for the classroom. If each space is served by a separate system, then the required outdoor ventilation rate of each system is 150 cfm and 750 cfm, respectively. This corresponds to a 15 percent outside air fraction in the office HVAC unit, and 50 percent in the classroom unit.
If both spaces are served by a central system, then the total supply will be (1,000 + 1,500) cfm = 2500 cfm. The required outdoor ventilation rate is (150 + 750) = 900 cfm total. The actual outdoor air ventilation rate for each space is:
Office outside air = 900 cfm x (1,000 cfm / 2,500 cfm) = 360 cfm
Classroom outside air = 900 cfm x (1,500 cfm / 2,500 cfm) = 540 cfm
While this simplistic analysis suggests that the actual outside air cfm to the classroom is less than design (540 cfm vs. 750 cfm), the analysis does not take credit for the dilution effect of the air recirculated from the office. The office is over-ventilated (360 cfm vs. 150 cfm) so the concentration of pollutants in the office return air is low enough that it can be used, along with the 540 cfm of outdoor air, to dilute pollutants in the classroom. The Energy Code allow this design provided that the system always delivers at least 750 cfm to the classroom (including transfer or recirculated air), and that any transfer air is free of unusual contaminants.
The exhaust ventilation requirements are new for the 2019 Energy Code. They are aligned with ASHRAE 62.1 and requires certain occupancy categories to be exhausted to the outdoors, as listed in Table 4-1. Exhaust flow rates must meet or exceed the minimum rates specified in 4-13. The spaces listed are expected to have contaminants not generally found in adjacent occupied spaces. Therefore, the air supplied to the space to replace the air exhausted may be any combination of outdoor air, recirculated air, and transfer air – all of which are expected to have low or zero concentration of the pollutants generated in the listed spaces. For example, the exhaust from a toilet room can draw air from either the outdoors, adjacent spaces, or from a return air duct or plenum. Because these sources of makeup air have essentially zero concentration of toilet-room odors, they are equally good at diluting odors in the toilet room.
The rates specified must be provided during all periods when the space is expected to be occupied, similar to the requirement for ventilation air.
Occupancy Category | Exhaust Rate (cfm/unit) | Exhaust Rate (cfm/ft2) | Air Class | Notes |
Arenas | - | 0.50 | 1 | B |
Art classrooms | - | 0.70 | 2 | |
Auto repair rooms | - | 1.5 | 2 | A |
Barber shops | - | 0.50 | 2 | |
Beauty and nail salons | - | 0.60 | 2 | |
Cells with toilet | - | 1.00 | 2 | |
Copy, printing rooms | - | 0.50 | 2 | |
Darkrooms | - | 1.00 | 2 | |
Educational science laboratories | - | 1.00 | 2 | |
Janitor closets, trash rooms, recycling | - | 1.00 | 3 | |
Kitchenettes | - | 0.30 | 2 | |
Kitchens – commercial | - | 0.70 | 2 | |
Locker rooms for athletic or industrial facilities | - | 0.50 | 2 | |
All other locker rooms | - | 0.25 | 2 | |
Shower rooms | 20/50 | - | 2 | G, H |
Paint spray booths | - | - | 4 | F |
Parking garages | - | 0.75 | 2 | C |
Pet shops (animal areas) | - | 0.90 | 2 | |
Refrigerating machinery rooms | - | - | 3 | F |
Soiled laundry storage rooms | - | 1.00 | 3 | F |
Storage rooms, chemical | - | 1.50 | 4 | F |
Toilets – private | 25/50 | - | 2 | E |
Toilets – public | 50/70 | - | 2 | D |
Woodwork shop/classrooms | - | 0.50 | 2 |
Notes:
A – Stands where engines are run shall have exhaust systems that directly connect to the engine exhaust and prevent escape of fumes.
B – Where combustion equipment is intended to be used on the playing surface, additional dilution ventilation, source control, or both shall be provided.
C – Exhaust shall not be required where two or more sides comprise walls that are at least 50% open to the outside.
D – Rate is per water closet, urinal, or both. Provide the higher rate where periods of heavy use are expected to occur. The lower rate shall be permitted to be used otherwise.
E – Rate is for a toilet room intended to be occupied by one person at a time. For continuous systems operation during hours of use, the lower rate shall be permitted to be used. Otherwise, the higher rate shall be used.
F – See other applicable standards for exhaust rate.
G – For continuous system operation, the lower rate shall be permitted to be used. Otherwise, the higher rate shall be used.
H – Rate is per showerhead.
Source: California Energy Commission, 2022 Building Energy Efficiency Standards, Table 120.1-B
This section contains air classification, a process that assigns an air class number based on the occupancy category then sets limits on transferring or recirculating that air. This offers designers clear guidance on what can and cannot be used for transfer, makeup, or recirculation air. In the Energy Code, the past, transfer air was allowed as long as it did not have “unusual sources of indoor air contaminants,” which left the enforcement of this rule to be arbitrary. Now, all spaces listed in Table 4-12 are assigned an air class and specific direction is given for each class, which is in alignment with ASHRAE 62.1.
Class 1: This class consists of air with low contaminant concentration, low sensory-irritation intensity, and inoffensive odor, suitable for recirculation or transfer to any space. Some examples include classrooms, lecture halls, and lobbies.
Class 2: This class consists of air with moderate contaminant concentration, mild sensory-irritation intensity, or mildly offensive odors. Class 2 air is suitable for recirculation or transfer to any space with Class 2 or Class 3 air, and that is utilized for the same or similar purpose and involves the same or similar pollutant sources. Class 2 air may be transferred to toilet rooms and to any Class 4 air occupancies. Class 2 air is not suitable for recirculation or transfer to dissimilar spaces with Class 2 or Class 3 air. It is also not suitable in spaces with Class 1 air, unless the Class 1 space uses an energy recovery device, then recirculation from leakage carryover or transfer from the exhaust side is permitted. In this case the amount of Class 2 air allowed to be transferred or recirculated shall not exceed 10 percent of the outdoor air intake flow. Thus, HVAC systems serving spaces with Class 2 air shall not share the same air handler as spaces with Class 1 air. Some examples include warehouses, restaurants, and auto repair rooms.
Class 3: This class consists of air with significant contaminant concentration, significant sensory-irritation intensity, or offensive odor that is suitable for recirculation within the same space. Recirculation of Class 3 air is only permitted within the space of origin. It is not suitable for recirculation or transfer to any other spaces. However, when a space uses an energy recovery device, then recirculation from leakage carryover or transfer from the exhaust side of the energy recovery device is permitted. In this case the amount of Class 3 air allowed to be transferred or recirculated shall not exceed 5 percent of the outdoor air intake flow. HVAC systems serving spaces with Class 3 air shall not share the same air handler serving spaces with Class 1 or Class 2 air. Some examples include general manufacturing (excludes heavy industrial and processes using chemicals) and janitor closets.
Class 4: This class consist of air with highly objectionable fumes or gases, as well as potentially dangerous particles, bioaerosols, or gases at concentrations high enough to be considered harmful. Class 4 air is not suitable for recirculation or transfer within the space or to any other space. No leakage of Class 4 air from energy recovery devices is allowed. Some examples include spray paint booths and chemical storage rooms.
In addition to Tables 4-12 and 4-13, the Energy Code also include air classifications for specific airstreams and sources as detailed in Table 4-14. In the event that Tables 4-12, 4-13 and 4-14 do not list the space or location, the air classification of the most similar space listed in terms of occupant activities or building construction shall be used.
Description | Air Class |
Diazo printing equipment discharge | 4 |
Commercial kitchen grease hoods | 4 |
Commercial kitchen hoods other than grease | 3 |
Laboratory hoods | 4a |
Hydraulic elevator machine room | 2 |
a. Air Class 4 unless determined otherwise by the Environmental Health and Safety professional responsible to the owner or to the owner’s designee.
Source: California Energy Commission, 2022 Building Energy Efficiency Standards, Table 120.1-C
For ancillary spaces that are designated as Class 1 air but support a Class 2 air space, re-designation of Class 1 air to Class 2 air for ancillary spaces to Class 2 areas is allowed. For example, a bank lobby is designated as Class 1 while bank vaults or safety deposit areas are designated at Class 2. The ancillary space to the bank safety deposit area can be re-designated to Class 2 from Class 1.
The Energy Code allow air to be directly transferred from one space to another to meet part of the ventilation supply, provided the total outdoor quantity required by all spaces served by the building’s ventilation system is supplied by the mechanical systems. This method can be used for any space, but is particularly applicable to conference rooms, toilet rooms, and other rooms that have high ventilation requirements. Transfer air may be a mixture of air from multiple spaces or locations, in which case the air mixture must be classified at the mixed highest classification. Transfer air must meet the requirements of air classification and recirculation limitations, as described above.
Air may be transferred using any method that ensures a positive airflow. Examples include dedicated transfer fans, exhaust fans, and fan powered VAV boxes. A system having a ducted return may be balanced so that air naturally transfers into the space. Exhaust fans serving the space may discharge directly outdoors, or into a return plenum. Transfer systems should be designed to minimize recirculation of transfer air back into the space; duct work should be arranged to separate the transfer air intake and return points.
When each space in a two-space building is served by a separate constant volume system, the calculation and application of ventilation rate is straightforward, and each space will always receive its design outdoor air quantity. However, a central system serving both spaces does not deliver the design outdoor air quantity to each space. Instead, one space receives more than its allotted share, and the other less. This is because some spaces have a higher design outdoor ventilation rate and/or a lower cooling load relative to the other space.
When a return plenum is used to distribute outside air to a zonal heating or cooling unit, the outside air supply must be connected either:
- Within 5 ft. of the unit; or
- Within 15 ft. of the unit, with the air directed substantially toward the unit, and with a discharge velocity of at least 500 ft per minute.
Water source heat pumps and fan coils are the most common application of this configuration. The unit fans should be controlled to run continuously during occupancy in order for the ventilation air to be circulated to the occupied space.
Not all spaces are required to have a direct source of outdoor air. Transfer air is allowed from adjacent spaces with direct outdoor air supply if the system supplying the outdoor air is capable of supplying the required outdoor air to all spaces at the same time. Air classification and recirculation limitations will apply, as explained above. An example of an appropriate use of transfer would be in buildings having central interior space-conditioning systems with outdoor air supply, and zonal units on the perimeter without a direct outdoor air supply.
Except for systems employing Energy Commission-certified DCV devices or space occupancy sensors, the Energy Code requires that the minimum rate of outdoor air calculated per §120.1(c)3 be provided to each space at all times, when the space is normally occupied according to §120.1(d)1 For spaces served by VAV systems, the minimum supply setting of each VAV box should be no less than the design outdoor ventilation rate calculated for the space, unless transfer air is used. If transfer air is used, the minimum box position, plus the transfer air, must meet the minimum ventilation rate.
The design outdoor ventilation rate at the system level must always be maintained when the space is occupied, even when the fan has modulated to its minimum capacity §120.1(d)1 Section 4.3.13 describes mandated acceptance test requirements for outside air ventilation in VAV air handling systems where the minimum outside air will be measured at full flow with all boxes at minimum position.
Figure 4-5 shows a typical VAV system. In standard practice, the testing and balancing contractor sets the minimum position setting for the outdoor air damper during construction. It is set under the conditions of design airflow for the system and remains in the same position throughout the full range of system operation, which does not meet code. As the system airflow drops, so will the pressure in the mixed air plenum. A fixed position on the minimum outdoor air damper will produce a varying outdoor airflow. Figure 4-5 shows this effect will be approximately linear (in other words, outdoor air airflow will drop directly in proportion to the supply airflow).
The following paragraphs present several methods used to dynamically control the minimum outdoor air in VAV systems.
Care should be taken to reduce the amount of outdoor air provided when the system is operating during the weekend or after hours with only a fraction of the zones active. Section 120.2(g) requires provision of “isolation zones” of 25,000 sq. ft. or less, which can be accomplished by having the VAV boxes return to fully closed when their associated zone is in unoccupied mode. When a space or group of spaces is returned to occupied mode (e.g., through off-hour scheduling or a janitor’s override), only the boxes serving those zones need to be active. During this period when not all the zones are occupied, the ventilation air can be reduced to the required ventilation air of just those zones that are active. If all zones are of the same occupancy type (e.g., private offices), simply assign a floor area to each isolation zone and prorate the minimum ventilation area by the ratio of the sum of the floor areas presently active divided by the sum of all the floor areas served by the HVAC system.
Figure 4-5: VAV Reheat System with a Fixed Minimum Outdoor Air Damper Set Point
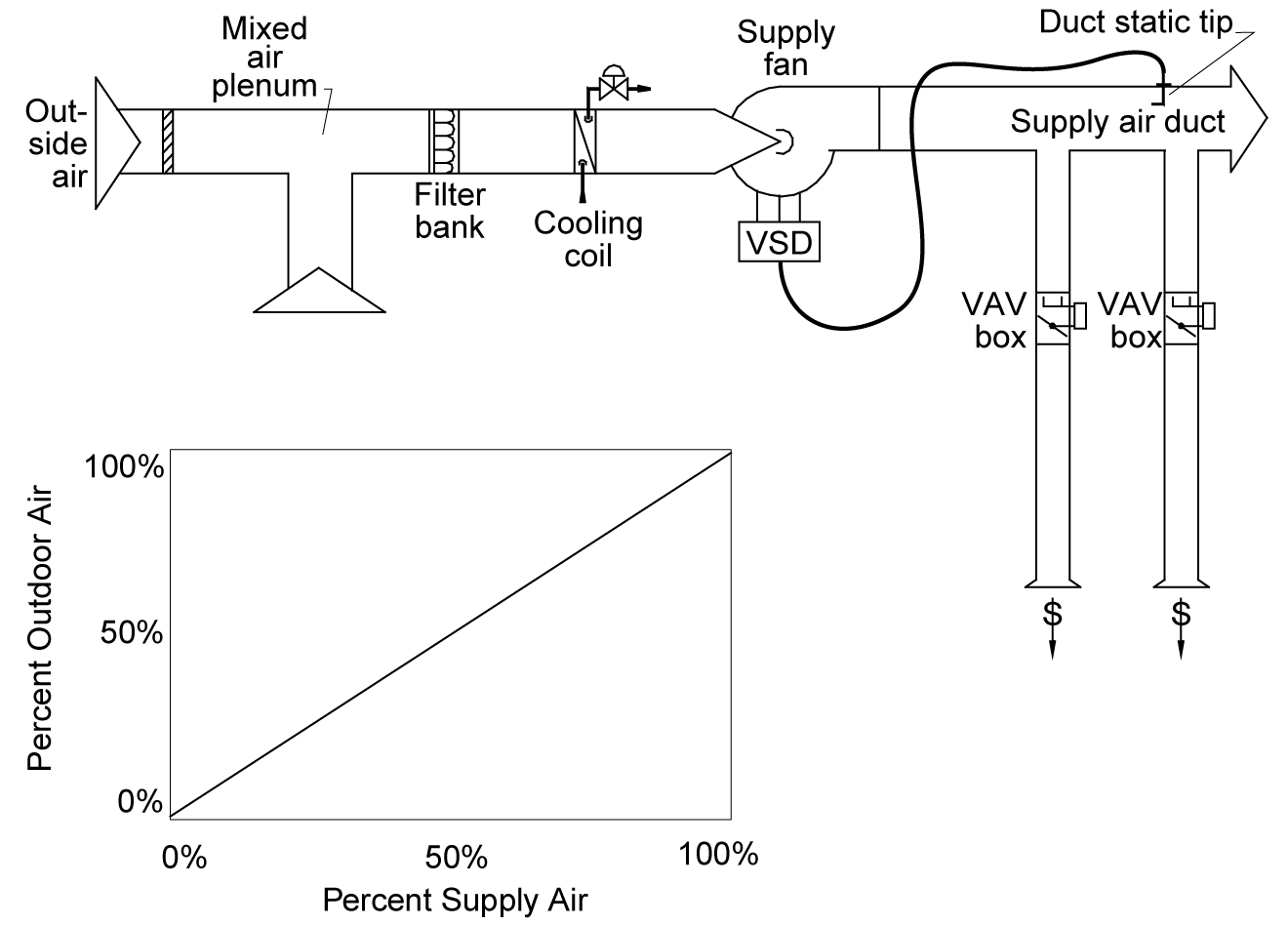
This method does not comply with the Energy Code. The airflow at a fixed minimum damper position will vary with the pressure in the mixed air plenum. It is explicitly prohibited in §120.1(f)2.
This method complies with the Energy Code. An inexpensive enhancement to the fixed damper set point design is the dual minimum set point design, commonly used on some packaged AC units. The minimum damper position is set proportionally based on fan speed or airflow between a set point determined when the fan is at full speed (or airflow) and minimum speed (or airflow). This method complies with the Energy Code but is not accurate over the entire range of airflow rates or when wind or stack effect pressure fluctuates. With DDC, this design has a relatively low cost.
The energy balance method uses temperature sensors located outside, as well as in the return and mixed air plenums to determine the percentage of outdoor air in the supply air stream. The outdoor airflow is then calculated using the equations shown in Figure 4-6. This method requires an airflow monitoring station on the supply fan.
While technically feasible, it may be difficult to meet the outside air acceptance requirements with this approach because:
1 This was the subject of ASHRAE Research Project 1045-RP, “Verifying Mixed Air Damper Temperature and Air Mixing Characteristics.” Unless the return is over the outdoor air there are significant problems with stratification or airstream separation in mixing plenums.
Figure 4-6: Energy Balance Method of Controlling Minimum Outdoor Air
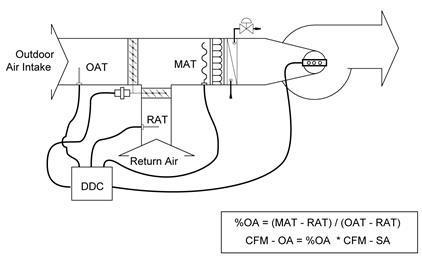
This method is also technically feasible but will likely not meet the acceptance requirements because the cumulative error of the two airflow measurements can be large, particularly at low supply/return airflow rates. It only works theoretically when the minimum outdoor air rate equals the rate of air required to maintain building pressurization (the difference between supply air and return air rates). Return fan tracking (Figure 4-7) uses airflow monitoring stations on both the supply and return fans. The theory behind this is that the difference between the supply and return fans should be made up by outdoor air and controlling the flow of return air forces more ventilation into the building. Several problems occur with this method:
- The relative accuracy of airflow monitoring stations is poor, particularly at low airflows
- The high cost of airflow monitoring stations
- Building pressurization problems unless the ventilation air is equal to the desired building exfiltration plus the building exhaust
ASHRAE research has also demonstrated that in some cases this arrangement can cause outdoor air to be drawn into the system through the exhaust dampers due to negative pressures at the return fan discharge.
Figure 4-7: Return Fan Tracking
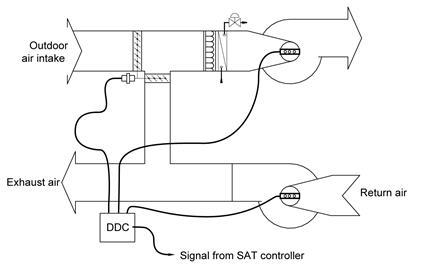
This method is technically feasible but will likely not meet the acceptance requirements, depending on the airflow measurement technology. Most airflow sensors will not be accurate within a 5 to 15 percent turndown (the normal commercial ventilation range). Controlling the outdoor air damper by direct measurement with an airflow monitoring station (Figure 4-8) can be an unreliable method. Its success relies on the turndown accuracy of the airflow monitoring station. Depending on the loads in a building, the ventilation airflow can be between 5 and 15 percent of the design airflow. If the outdoor airflow sensor is sized for the design flow for the airside economizer, this method has to have an airflow monitoring station that can turn down to the minimum ventilation flow (between 5 and 15 percent). Of the different types available, only a hot-wire anemometer array is likely to have this low-flow accuracy while traditional pitot arrays will not. One advantage of this approach is that it provides outdoor airflow readings under all operating conditions, not just when on minimum outdoor air. For highest accuracy, provide a damper and outdoor air sensor for the minimum ventilation air that is separate from the economizer outdoor air intake.
Figure 4-8: Airflow Measurement of 100 Percent Outdoor Air
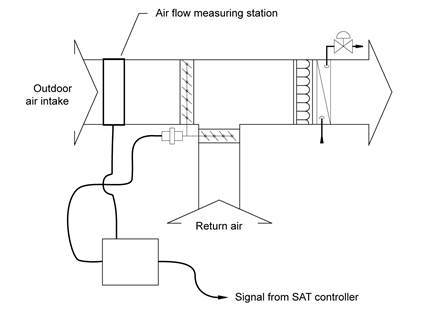
This method complies with the Energy Code, but it is expensive and may require additional space. An airflow sensor and damper are required since fan airflow rate will vary, as mixed air plenum pressure varies. The injection fan method (Figure 4-9) uses a separate outdoor air inlet and fan sized for the minimum ventilation airflow. This inlet contains an airflow monitoring station, and a fan with capacity control (e.g., discharge damper; variable frequency drives [VFD]), which is modulated as required to achieve the desired ventilation rate. The discharge damper is required to shut off the intake when the air handling unit (AHU) is off, and also to prevent excess outdoor air intake when the mixed air plenum is significantly negative under peak conditions. The fan is operating against a negative differential pressure and thus cannot stop flow just by slowing or stopping the fan. Though effective, the cost of this method is high and often requires additional space for the injection fan assembly.
Figure 4-9: Injection Fan with Dedicated Minimum Outdoor Air Damper
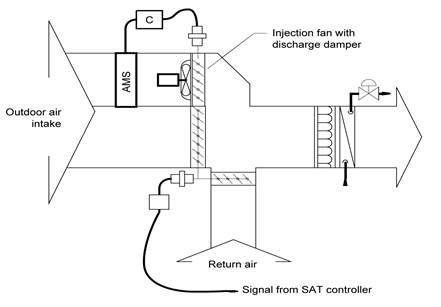
This approach is low cost and takes little space. It can be accurate if the differential set point corresponding to the minimum outdoor air rate is properly set in the field. An inexpensive but effective design uses a minimum ventilation damper with differential pressure control (Figure 4-10). In this method, the economizer damper is broken into two pieces: a small two position damper controlled for minimum ventilation air and a larger, modulating, maximum outdoor air damper that is used in economizer mode. A differential pressure transducer is placed across the minimum outdoor air damper. During start-up, the air balancer opens the minimum outside air (OA) damper and return air damper, closes the economizer OA damper, runs the supply fan at design airflow, measures the OA airflow and adjusts the minimum OA damper position until the OA airflow equals the design minimum OA airflow. The linkages on the minimum OA damper are then adjusted so that the current position is the “full open” actuator position. At this point the design pressure (DP) across the minimum OA damper is measured. This value becomes the DP set point. The principle used here is that airflow is constant across a fixed orifice (the open damper) at fixed DP.
As the supply fan modulates when the economizer is off, the return air damper is controlled to maintain the DP setpoint across the minimum ventilation damper.
The main downside of this method is the complexity of controls and the potential problems determining the DP setpoint in the field. It is often difficult to measure the outdoor air rate due to turbulence and space constraints.
Figure 4-10: Minimum Outdoor Air Damper with Pressure Control
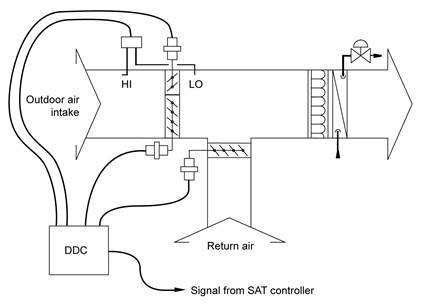
Example 4-10: Minimum VAV cfm
Question
If the minimum required ventilation rate for a space is 150 cfm, what is the minimum allowed airflow for its VAV box when the percentage of outdoor air in the supply air is 20 percent?
Answer
The minimum allowed airflow may be as low as 150 cfm provided that enough outdoor air is supplied to all spaces combined to meet the requirements of §120.1(b)2 for each space individually.
§120.1(d)2 and §160.2(c)5B
Since many indoor air pollutants are out gassed from the building materials and furnishings, the Energy Code requires that buildings having a scheduled operation be purged before occupancy per §120.1(d)2. Immediately prior to occupancy, outdoor ventilation must be provided in an amount equal to the lesser of:
- The minimum required ventilation rate for 1 hour
- Three complete air changes
Either criterion can be used to comply with the Energy Code. Three complete air changes mean an amount of ventilation air equal to three times the volume of the occupied space. This air may be introduced at any rate provided for and allowed by the system, so that the actual purge period may be less than an hour.
A pre-occupancy purge is not required for buildings or spaces that are not occupied on a scheduled basis, such as storage rooms. Also, a purge is not required for spaces provided with natural ventilation.
Where pre-occupancy purge is required, it does not have to be coincident with morning warm-up (or cool-down). The simplest way to integrate the two controls is to schedule the system to be occupied one hour prior to the actual time of anticipated occupancy. This allows the optimal start, warm-up, or pull-down routines to bring the spaces up to (or down to) desired temperatures before opening the outdoor air damper for ventilation. This will reduce the required system heating capacity and ensure that the spaces will be at the desired temperatures and fully purged at the start of occupancy.
However, for spaces with occupancy controls which turn ventilation off when occupancy is not sensed, care must be taken in specifying controls and control sequences that the lack of sensed occupancy does not disable or override ventilation during the pre-occupancy purge period.
Figure 4-11: Pre-Occupancy Purge Flowchart
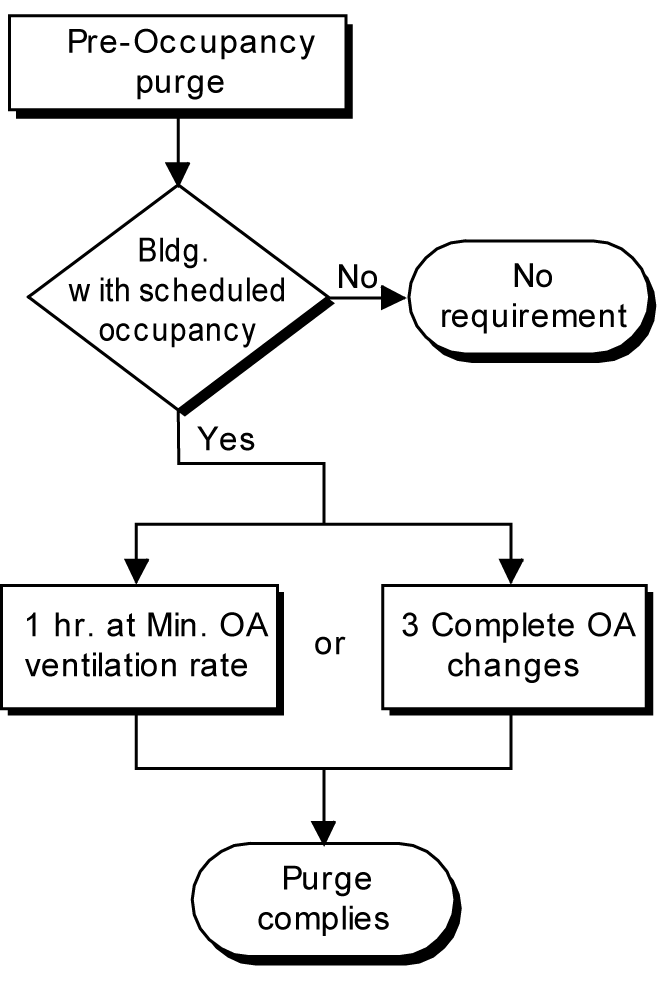
Example 4-11: Purge Period
Question
What is the length of time required to purge a space 10 ft high with an outdoor ventilation rate of 1.5 cfm/sq ft?
Answer
For three air changes, each sq ft of space must be provided with:
OA volume = 3 x 10 = 30 cf/ft²
At a rate of 1.5 cfm/sq ft, the time required is:
Time = 30 cf/ft² / 1.5 cfm/ft² = 20 minutes
Example 4-12: Purge with Natural Ventilation
Question
In a building with natural ventilation, do the windows need to be left open all night to accomplish a building purge?
Answer
No. A building purge is required only for buildings with mechanical ventilation systems.
Example 4-13: Purge with Occupancy Timer
Question
How is a purge accomplished in a building without a regularly scheduled occupancy, whose system operation is controlled by an occupancy sensor?
Answer
This building is most likely 24/7 accessible and a purge requirement would not apply for this building. The occupancy sensors and manual timers can only be used to control ventilation systems in buildings that are intermittently occupied without a predictable schedule.
§120.1(d)3 and 4 and §160.2(c)5C
Demand controlled ventilation systems reduce the amount of ventilation supply air in response to a measured level of carbon dioxide (CO2) in the breathing zone. The Energy Code only permit CO2 sensors for the purpose of meeting this requirement; volatile organic compounds (VOC) and so-called “indoor air quality(IAQ)” sensors are not approved as alternative devices to meet this requirement. The Energy Code only permit DCV systems to vary the ventilation component that corresponds to occupant bioeffluents (this is the basis for the 15 cfm/person portion of the ventilation requirement). The purpose of CO2 sensors is to track occupancy in a space; however, there are many factors that must be considered when designing a DCV system. There is often a lag time in the detection of occupancy through the build-up of CO2. This lag time may be increased by any factors that affect mixing, such as short circuiting of supply air or inadequate air circulation, as well as sensor placement and sensor accuracy. Build-up of odors, bioeffluents, and other health concerns may also delay changes in occupancy. Therefore, the designers must be careful to specify CO2 based DCV systems that are designed to provide adequate ventilation to the space by ensuring proper mixing, avoiding short circuiting, and proper placement and calibration of the sensors.
- An air economizer
- Modulating outside air control
- Design outdoor airflow rate greater than 3,000 cfm
This relates to the fact that spaces with high exhaust requirements won’t be able to provide sufficient turndown to justify the cost of the DCV controls. An example of this is a restaurant seating area where the seating area air is used as make-up air for the kitchen hood exhaust.
This exception recognizes that some spaces may need additional ventilation due to contaminants that are not occupant borne. It addresses spaces like theater stages where theatrical fog may be used or movie theater lobbies where unvented popcorn machines may be emitting odors and vapors into the space in either case justifying the need for higher ventilation rates. DCV devices shall not be installed in spaces included in this exception.
This recognizes the fact that DCV devices may not be cost effective in small spaces such as a 15 ft. by 10 ft. conference room or spaces with only a few occupants at design conditions.
Although not required, the Energy Code permit design professionals to apply DCV on any intermittently occupied spaces served by either single-zone or multiple-zone equipment. §120.1(c)3 requires a minimum of 15 cfm of outdoor air per person multiplied by the expected number of occupants. However, it must be noted that these are minimum ventilation levels, and the designers may specify higher ventilation levels if there are health related concerns that warrant higher ventilation rates.
CO2 based DCV is based on several studies (Berg-Munch et al. 1986, Cain et al. 1983, Fanger 1983 and 1988, Iwashita et al. 1990, Rasmussen et al. 1985) which concluded that about 15 cfm of outdoor air ventilation per person will control human body odor such that roughly 80 percent of unadapted persons (visitors) will find the odor to be at an acceptable level. As activity level increases and bioeffluents increase, the rate of outdoor air required to provide acceptable air quality increases proportionally, resulting in the same differential CO2 concentration.
A CO2 sensor only tracks indoor contaminants that are generated by occupants themselves and, to a lesser extent, their activities. It will not track other pollutants, particularly volatile organic compounds that off-gas from furnishings and building materials. Hence, where permitted or required by the Energy Code, DCV systems cannot reduce the outdoor air ventilation rate below the lowest rate listed in Table 4-12 (typically 0.15 cfm/ft2) during normally occupied times.
DCV systems save energy if the occupancy varies significantly over time. Hence, they are most cost effective when applied to densely occupied spaces like auditoriums, conference rooms, lounges, or theaters. Because DCV systems must maintain the lowest ventilation rate listed in Table 4-12, they will not be applicable to sparsely occupied buildings such as offices where the floor rate always exceeds the minimum rate required by the occupants (See Table 4-1).
- Sensors must be provided in each room served by the system that has a design occupancy of 40 sq. ft. per person or less, with no less than one sensor per 10,000 sq. ft. of floor space. When a zone or a space is served by more than one sensor, signals from any sensor indicating that CO2 is near or at the set point within a space, must trigger an increase in ventilation to the space. This requirement ensures that the space is adequately ventilated in case a sensor malfunctions. Design professionals should ensure that sensors are placed throughout a large space, so that all areas are monitored by a sensor.
- The CO2 sensors must be located in the breathing zone (between three and six ft. above the floor or at the anticipated height of the occupant’s head). Sensors in return air ducts are not allowed since they can result in under-ventilation due to CO2 measurement error caused by short-circuiting of supply air into return grilles and leakage of outdoor air (or return air from other spaces) into return air ducts.
- The ventilation must be maintained that will result in a concentration of CO2 at or below 600 ppm above the ambient level. The ambient levels can either be assumed to be 400 ppm or dynamically measured by a sensor that is installed within four feet of the outdoor air intake. At 400 ppm outside CO2 concentration, the resulting DCV CO2 set point would be 1000 ppm. (A 600-ppm differential is less than the 700 ppm that corresponds to the 15 cfm/person ventilation rate. This provides a margin of safety against sensor error, and because 1000 ppm CO2 is a commonly recognized guideline value and referenced in earlier versions of ASHRAE Standard 62.) Note that the 1,000 PPM setpoint required by Title 24 is not the same approach to DCV as specified in the current version of ASHRAE 62.1 or ASHRAE 90.1 which do not have a fixed CO2 target for all spaces, and ASHRAE Standards 90.1 and 62.1 have lower ventilation rates per person. ASHRAE Guideline 36-2021, High-Performance Sequences of Operation for HVAC Systems, contains separate sequences of operation for complying with Title 24 and ASHRAE 90.1-2019.
- Regardless of the CO2 sensor’s reading, the system is not required to provide more than the minimum ventilation rate required by §120.1(c)3. This prevents a faulty sensor reading from causing a system to provide more than the code required ventilation for system without DCV control. This high limit can be implemented in the controls.
- The system shall always provide a minimum ventilation of the sum of the minimum air rate for DCV for all rooms with DCV and the minimum air rate for all other spaces served by the system, as listed in Table 4-1. This is a low limit setting that must be implemented in the controls.
- The CO2 sensors must be factory-certified to have an accuracy within plus or minus 75 ppm at 600 and 1000 ppm concentration when measured at sea level and 25 degree Celsius (77 degrees F), factory calibrated or calibrated at start-up, and certified by the manufacturer to require calibration no more frequently than once every five years. A number of manufacturers now have self-calibrating sensors that either adjust to ambient levels during unoccupied times or adjust to the decrease in sensor bulb output through use of dual sources or dual sensors. For all systems, sensor manufacturers must provide a document to installers that their sensors meet these requirements. The installer must make this certification information available to the builder, building inspectors and, if specific sensors are specified on the plans, to plan checkers.
- When a sensor failure is detected, the system must provide a signal to reset the system to provide the minimum quantity of outside air levels required by §120.1(c)3 to the zone(s) serviced by the sensor at all times that the zone is occupied. This requirement ensures that the space is adequately ventilated in case a sensor malfunctions. A sensor that provides a high CO2 signal on sensor failure will comply with this requirement.
- For systems that are equipped with DDC to the zone level, the CO2 sensor(s) reading for each zone must be displayed continuously and recorded. The EMCS may be used to display and record the sensors’ readings. The display(s) must be readily available to maintenance staff so they can monitor the systems performance.
§120.1(d)5 and §160.2(c)5E; §120.3(e)3 and §160.3(a)2Diii
The use of occupant sensor ventilation control devices is mandated for spaces that are also required to use occupant sensing controls to meet the requirements for lighting shut-off controls per §130.1(c), example spaces include offices , multipurpose rooms 1,000 sq. ft. or less, classrooms, conference rooms, and other spaces where the space ventilation is allowed to be reduced to zero in Table 120.1-A (see note F in the right-hand column of the table).
The HVAC system shall be controlled by an occupancy sensing control that resets temperature setpoints and ventilation air in accordance with §120.1(d)5, and §120.2(e)3 when a space meets both the following conditions.
- §130.1(c) items 5,6, and 7 specifies that occupant sensing, as opposed to time-switch, is required to implement shutoff controls.
- Table 120.1-A specifies that ventilation air in the space is allowed to be reduced to zero when the space is in occupied standby mode.
The following table lists all the occupancy categories that meet both conditions above and thus are required to install occupied standby controls if the ventilation zone is serving only qualifying spaces. Note that the “Corridors” category is duplicated from the general category and offices are duplicated from the office category to other building types for clarity.
Occupancy Category |
Educational Facilities |
Lecture/postsecondary classroom |
Lecture hall (fixed seats) |
Music/theater/dance |
Multiuse assembly (only those less than 1,000 square feet) |
Corridors |
Office Space |
General |
Break rooms (lounges) |
Coffee Stations |
Conference/meeting |
Corridors |
Hotels, Motels, Resorts, Dormitories |
Common area corridors that provide access to guest rooms |
Multipurpose assembly (only those less than 1,000 square feet) |
Office Buildings |
Office space |
Breakrooms (lounges) |
Classrooms (professional training rooms) |
Conference rooms, multipurpose rooms |
Corridors |
Telephone/data entry |
Residential (based on TABLE 160.2-B) |
Multiuse Assembly (only those less than 1,000 square feet) |
Break Rooms |
Coffee Stations |
Conference / Meeting |
Corridors |
Telephone/data entry |
Source: California Energy Commission
Occupant sensor Ventilation control devices are used to implement “occupied standby control.” This control is used when the HVAC is scheduled to be ON, but occupancy sensors do not detect any activity in the spaces served by the HVAC zone. During occupied standby, zone temperatures are reset (higher cooling setpoint and lower heating setpoint) and during times when there is neither a call for cooling nor heating the ventilation air is shut off to the zone. When ventilation air is shut off to the zone, the ventilation system serving the zone shall reduce the system outside air by the same amount of outside air reduced at the individual zone. For systems using DOAS units, please see the special note at the end of this section.
Where occupant sensor ventilation control devices are employed (whether mandated or not) the controls must meet all of the following requirements:
- Sensors must meet the requirements of §110.9(b)4 and shall have suitable coverage to detect occupants in the entire space.
- Sensors that are used for lighting can be used for ventilation if the ventilation system is controlled directly from the occupant sensor and is not subject to daylighting control or other manual overrides.
- If a space conditioning system(s) serves several enclosed spaces, each space shall have its own occupant sensor and all sensors must indicate lack of occupancy before the zone airflow is cut off.
- The occupant sensor override of ventilation shall be disabled during preoccupancy purge (i.e., the terminal unit and central ventilation shall be active regardless of occupant status). Preoccupancy purge occurs during times that are scheduled to be unoccupied and the HVAC system is scheduled off and thus does not overlap with occupied standby periods.
- Occupant sensing controls shall indicate that a space or lighting zone is vacant in 20 minutes or less after no occupant activity is detected by any occupant sensors covering the space.
- When all the lighting zones served by the same space conditioning zone are vacant as indicated by the occupant sensing controls, the space conditioning zone enters occupied- standby mode.
Once a space conditioning zone enters occupied-standby mode, in 5 minutes or less, thermostatic setpoints are reset and mechanical ventilation to the zone shall be shut off until any room served by the space conditioning zone becomes occupied or until ventilation is needed to provide space heating or conditioning. Temperature setback can be achieved either by:- Automatically set up the operating cooling temperature set point by 2°F or more and set back the operating heating temperature set point by 2°F or more; or
- For multiple zone systems with Direct Digital Controls (DDC) to the zone level, set up the operating cooling temperature setpoint by 0.5°F or more and set back the operating heating temperature setpoint by 0.5°F or more.
Note: Steps 5-7 allows a time delay up to 25 minutes (20 minutes sensor time delay + 5 minute occupied standby time delay) after no occupant activity is detected in all lighting zones served by the space conditioning zone and before the ventilation to the rooms is shut off.
The ventilation zone may be serving more than one room, in which case all rooms served by the space conditioning zone must be sensed as unoccupied before the system is placed in occupied standby mode. The illustration below (Figure 4-12) provides an example of the sequence of events for two rooms (LZ1 and LZ2) served by one ventilation zone and how to occupant-sensing lighting controls relate to the HVAC ventilation controls.
8. Single zone systems when “floating” between a call for heating or cooling will be shut off. For multizone systems with outside airflow monitoring, when the system enters occupied standby and sets the zone airflow to zero, the system outside airflow can be reduced to account for the reduced need for outside air. ASHRAE Guideline 36-2021, High-Performance Sequences of Operation for HVAC Systems, provides operating sequences that include the specific instructions for resetting outside air amounts in response to a zone being placed in occupied standby while complying with the Title 24, part 6 minimum outside air flowrates for the other zones.
What is ASHRAE Guideline 36?
ASHRAE Guideline 36, High-Performance Sequences of Operation for HVAC Systems, provides peer-reviewed sequences of operation for HVAC systems, written in a format that can be readily implemented by building controls manufacturers and control system contractors. It is continuously updated by a large committee of engineers, manufacturers, scientists, and contractors following the rigorous ASHRAE public review process. These sequences are intended to maximize energy efficiency while maintaining good indoor air quality and comfort. The sequences have been configured and tested to provide control stability and real-time fault detection and diagnostics. Specifying Guideline 36 control sequences reduces risk of Energy Management Control System programming errors and provides a common set of terms and sequences to facilitate communication between specifiers, contractors, and operators.
Example 4-13
Question
If an HVAC zone is designed to serve an office space, conference room, corridor, and restrooms, does this configuration require occupied standby capabilities to shut off ventilation?
Answer
Yes.
Offices Spaces, Corridors, and Restrooms all require occupancy sensing controls under Section 130.1(c) AND are occupancy categories that can have their ventilation air reduced to zero when the space is in occupied-standby mode.
- Restrooms require occupant sensing controls under section 130.1(c)5.
- Small offices (250 square feet or less) require occupant sensing controls under 130.1(c)5.
- Large offices (250 square feet or greater) require occupant sensing controls under 130.1(c)6.
- Conference rooms of any size require occupant sensing controls under 130.1(c)5.
- Office Corridors require occupant sensing controls under sections 130.1(c)6.
While restrooms do not have minimum ventilation requirements, restroom ventilation air is pulled from corridors through their minimum exhaust requirements (see “Toilets-public” or “Toilets-private” under Table 120.1-B).
Corridors which provide that ventilation are subject to occupied-standby mode under Table 120.1-A, as are office spaces (as indicated by the note “F” Column).
Below is a limited excerpt from Table 120.1-A, those marked with “F” under the “Notes” column would require occupied standby mode:
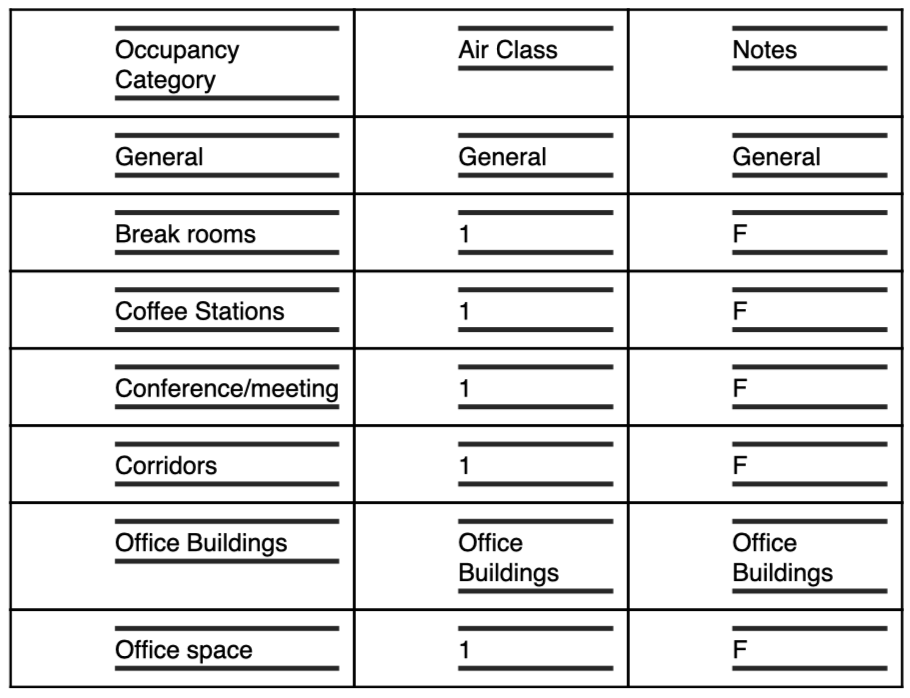
F – Ventilation air for this occupancy category shall be permitted to be reduced to zero when the space is in occupied mode.
Example 4-15
Question
If an HVAC zone is designed to serve both an office space and classrooms does this configuration require occupied standby capabilities to shut off ventilation?
Answer
No, for Pre-K and K-12 classrooms.
Yes, for most Higher Education and commercial training classrooms.
As noted in the previous example, the occupied standby mode requirements are triggered if the space is subject to have occupant sensing controls under 130.1(c) AND are occupancy categories that can have their ventilation air reduced to zero when the space is in occupied-standby mode under Table 120.1-A. While all classrooms are required occupant sensing controls under Section 130.1(c)5, only certain types of classrooms can reduce ventilation flow to zero when the space is in occupied-standby mode.
In the case of classrooms, pre-K and K-12 educational facilities and some specialized classrooms such as art classrooms do not require occupied standby while those intended for college, community college, business lectures, or classrooms do require them. Note that the space types listed under other building types “Offices” and “General” would still apply to Educational Facilities, as result offices and corridors in educational buildings which both are required to have occupancy sensing and are allowed to set ventilation to 0 during occupied standby would also be required to have occupied standby controls if all the spaces in a thermal zone qualify for occupied standby.
Below is a limited excerpt from Table 120.1-A, those marked with “F” under the “Notes” column require occupied standby mode:
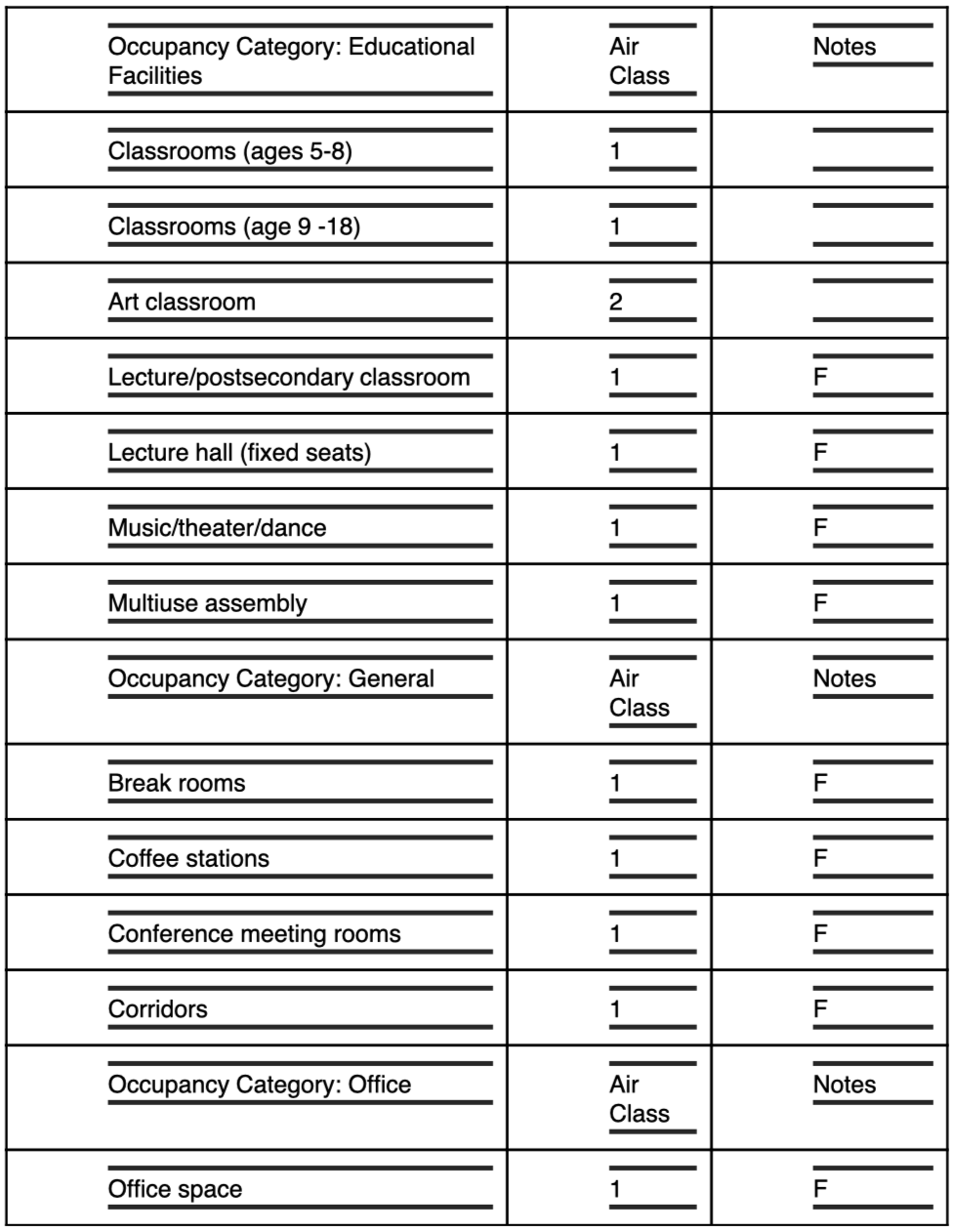
F – Ventilation air for this occupancy category shall be permitted to be reduced to zero when the space is in occupied-standby mode.
Example 4-16
Question 1
For thermal zones required to have occupant sensor ventilation controls, are these spaces allowed to set the ventilation rate to 0 during the preoccupancy ventilation purge period if there are no occupants sensed in the thermal zone?
Answer 1
No. Preoccupancy controls (§120.1(d)), ventilate the building “during the 1-hour period immediately before the building is normally occupied.” Occupant sensor control devices (§120.1(d)5E), in contrast operate “When the zone is scheduled to be occupied and occupant sensing controls in all rooms and areas served by the zone indicate the spaces are unoccupied, ” To be doubly clear, Section 120.1(d)5D says, “One hour prior to normal scheduled occupancy, occupant sensor ventilation control shall allow pre- occupancy purge as described in Section 120.1(d)2. See Figure 4-12 even though both spaces are vacant, and lights are out in these spaces, the space is being ventilated during the pre-occupancy purge period. This pre-occupancy purge period ventilated the space prior to the day’s scheduled occupancy dilute site generated pollutants that have built up over night.
Question 2
For a thermal zone required to have occupant sensor ventilation controls, what is the range of time delays allowed between all occupancy sensors in the zones sensing vacancy and the control shutting off ventilation air to the zone?
Answer 2
Between 0 and 25 minutes. For the control with the shortest time delay, one could directly receive the output of the occupancy sensors and place the system in occupied standby mode whenever all the sensors do not receive a signal indicating occupancy. However, this control would have a lot of false vacancy signals as the occupant sensors are not able to detect movement continuously in occupied spaces and would be cycling the system back and forth between occupied standby and occupied. There are some HVAC designers that directly take the occupant sensor signal without the time delay built into the occupancy sensor and the program the system shut off ventilation air after a 5- minute time delay. It is also acceptable to take the lighting occupant sensor control signal that includes the lighting system time delay which is allowed to be set to as long as 20 minutes. This approach is used when the HVAC control system is taking the on/off signal from an extra set of dry contracts on the lighting occupant sensor. The HVAC system designer is allowed to take this lighting system signal which included the lighting control time delay and add on an extra 5-minute time delay before resetting the system setpoints and shutting off the ventilation air to zero.
Figure 4-12 Control Sequence Diagram of
Occupied Standby Control of HVAC Thermal Zone Serving Two Lighting Zones (LZ1 and LZ2)
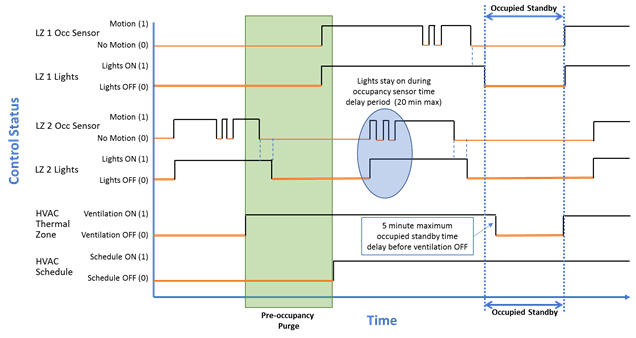
Source: California Energy Commission
Special Note for Dedicated Outdoor Air Systems (DOAS)
HVAC zones utilizing DOAS units must still adhere to occupied standby control requirements under certain conditions.
For example, if a DOAS unit is used to ventilate multiple spaces without any downstream modulation controls then the entire DOAS unit is treated as one ventilation zone for the purposes of the occupied standby requirement and would only be subject to use occupied-standby controls if ALL ventilated spaces were listed under Table 4-4. To comply, the unit would be required to implement occupied standby controls to reduce ventilation to zero (i.e., shut off the DOAS unit) and operate independent of the space-conditioning setpoints.
Additionally, if a DOAS unit features any ventilation modulation controls downstream of the DOAS unit, then any branches of ventilation air with modulation control shall be considered a separate ventilation zone for the purposes of this requirement.
§120.1(d)1 and §160.2(c)5A
While §120.1(d) requires that ventilation be continuous during normally occupied hours when the space is usually occupied, Exception 2 allows the ventilation to be disrupted for not more than 30 minutes at a time. In this case the ventilation rate during the time the system is ventilating must be increased so the average rate over the hour is equal to the required rate.
It is important to review any related ventilation and fan cycling requirements in Title 8, which is the Division of Occupational Safety and Health (Cal/OSHA) regulations. Section 5142 specifies the operational requirements related to HVAC minimum ventilation. It states:
Operation:
Title 8 Section 5142(a)(1) refers to Title 24, Part 2 (the California Building Code) for the minimum ventilation requirements. Section 1203 in the California Building Code specifies the ventilation requirements, but simply refers to the California Mechanical Code, which is Title 24, Part 4.
Chapter 4 in the California Mechanical Code specifies the ventilation requirements. Section 402.3 states, “The system shall operate so that all rooms and spaces are continuously provided with the required ventilation rate while occupied.” Section 403.5.1 states, “Ventilation systems shall be designed to be capable of providing the required ventilation rates in the breathing zone whenever the zones served by the system are occupied, including all full and part-load conditions.” The required ventilation rates are thus not required whenever the zones are unoccupied. This section affirms that ventilation fans may be turned off during unoccupied periods. In addition, Section 403.6 states, “The system shall be permitted to be designed to vary the design outdoor air intake flow or the space or zone airflow as operating conditions change.” This provides further validation to fan cycling as operating conditions change between occupied and unoccupied. A vacant zone has no workers present and is thus not subject to working hour’s requirements until the zone is actually occupied by a worker. Finally, Title 24, Part 4, states; “Ventilation air supply requirements for occupancies regulated by the California Energy Commission are found in the California Energy Code.” Thus, it refers to Title 24, Part 6 as the authority on ventilation.
Title 8 Section 5142(a)(2) states, “The HVAC system shall be operated continuously during working hours.” This regulation does not indicate that the airflow, cooling, or heating needs to be continuous. If the HVAC system is designed to maintain average ventilation with a fan cycling algorithm and is active in that mode providing average ventilation air as required during working hours, it is considered to be operating continuously per its mode and sequence. During unoccupied periods, the HVAC system is turned off except for setback and it no longer operates continuously. During the occupied period, occupant sensors or CO2 sensors in the space provide continuous monitoring and the sequence is operating, cycling the fan and dampers as needed to maintain the ventilation during the occupied period. The HVAC system is operating with the purpose of providing ventilation, heating, and cooling continuously during the working hours. The heater, air conditioner, fans, and dampers all cycle on and off subject to their system controls to meet the requirements during the working hours.
Exceptions A, B, and C to Title 8 Section 5142(a)(2) all refer to a complete system shutdown where the required ventilation is not maintained.
Example 4-14
Question
Does a single zone air-handling unit serving a 2,000 sq. ft. auditorium with fixed seating for 240 people require DCV?
Answer
Since the space has an occupant load factor of 8.3 sq. ft. per person (2,000 sq. ft. per 240 people), it meets the 40 sq. ft./person or less requirement triggering demand control ventilation if it has at least one of the following:
- -Air economizer
- -Modulating outside air control -Design outdoor airflow greater than 3,000 cfm
A single CO2 sensor could be used for this space provided it is certified by the manufacturer to cover 2,000 sq. ft. of space. The sensor must be placed directly in the space.
Example 4-15
Question
If two separate units are used to condition the auditorium in the previous example, is DCV required?
Answer
Yes, for each system that meets the criteria above.
Example 4-16
Question
Does the 2,000 sq ft auditorium in the previous examples require both DCV per Section 4.3.9. and occupant sensor ventilation control devices per Section 4.3.10?
Answer
No, only DCV is required because occupant sensor ventilation control devices are only required for spaces such as offices 250 sq ft or less, multipurpose rooms 1,000 sq ft or less, classrooms, conference rooms, or restrooms.
Example 4-17
Question
If a central AHU supplies five zones of office space (with a design occupant density of 100 sq ft per person and two zones with conference rooms (with a design occupant density of 35 sq ft per person) is it required to have demand-controlled ventilation and if so, on which zones?
Answer
If the AHU has DDC controls to the zone and an airside economizer it is required to have DCV controls in both of the conference room zones.
The minimum OSA will be set for 0.15 cfm/ft² times the total area of all seven zones (the office and conference room zones) and the maximum required OSA does not need to exceed the sum of 0.15 cfm/ft² for the five office zones plus 15 cfm per person for the two conference rooms.
Some VAV systems provide conditioned supply air, either heated or cooled, through a single set of ducting. These systems are called VAV changeover systems or, perhaps more commonly, variable volume and temperature (VVT™) systems, named after a control system, distributed by Carrier Corp. In the event that heating is needed in some spaces at the same time that cooling is needed in others, the system must alternate between supplying heated and cooled air. When the supply air is heated, for example, the spaces requiring cooling are isolated (cut off) by the VAV dampers and must wait until the system switches back to cooling mode. In the meantime, they are generally not supplied with ventilation air.
Systems of this type may not meet the ventilation requirements if improperly applied. Where changeover systems span multiple orientations, the designer must make control provisions to ensure that no zone is shut off for more than 30 minutes at a time and that ventilation rates are increased during the remaining time to compensate. Alternatively, minimum damper position or airflow set points can be set for each zone to maintain supply air rates, but this can result in temperature control problems since warm air will be supplied to spaces that require cooling, and vice versa. Changeover systems that are applied to a common building orientation (e.g., all east or all interior) are generally the most successful since zones will usually have similar loads, allowing minimum airflow rates to be maintained without causing temperature control problems.
Section 120.1(c) specifies the minimum required outdoor ventilation rate but does not restrict the maximum. However, if the designer elects to have the space-conditioning system operate at a ventilation rate higher than required by the Energy Code, then the space-conditioning system must be adjustable. This way so the ventilation rate can be reduced in the future to 1) the amount required by the Energy Code, or 2) the rate required for make-up of exhaust systems that are required for a process, for control of odors, or for the removal of contaminants within the space §120.1(f).
In other words, a system can be designed to supply higher than minimum outside air volumes, provided dampers or fan speed can be adjusted to allow no more than the minimum volume if desired in the future. The Energy Code preclude a system designed for 100 percent outdoor air, with no provision for any return air, unless the supply air quantity can be adjusted to be equal to the designed minimum outdoor air volume. The intent is to prevent systems from being designed that will permanently over-ventilate spaces.
The Energy Code has acceptance test requirements for:
- Ventilation system time controls §120.5(a)2 and NA7.5.2.
These test requirements are described in Chapter 13 and the Reference Nonresidential Appendix NA7.5. They are described briefly in the following paragraphs.
Example 4-18: Maintenance of Ventilation System
Question
In addition to these commissioning requirements for the ventilation system, are there any periodic requirements for inspection?
Answer
The Energy Code do not contain any such requirements since they apply to the design and commissioning of buildings, not to later operation. However, Section 5142 of the General Industry Safety Orders, Title 8, California Safety Code: Mechanically Driven Heating, Ventilating and Air Conditioning (HVAC) Systems to Provide Minimum Building Ventilation, states the following:
Inspection and Maintenance
(1) The HVAC system shall be inspected at least annually, and problems found during these inspections shall be corrected within a reasonable time.
(2) Inspections and maintenance of the HVAC systems shall be documented in writing. The employer shall record the name of the individual(s) inspecting and/or maintaining the system, the date of the inspection and/or maintenance, and the specific findings and actions taken. The employer shall ensure that such records are retained for at least five years.
(3) The employer shall make all records required by this section available for examination and copying, within 48 hours of a request, to any authorized representative of the Division (as defined in Section 3207 of Title 8), to any employee of the employer affected by this section, and to any designated representative of said employee of the employer affected by this Section.
Ventilation airflow must be certified to be measured within 10 percent of the design airflow quantities at two points of operation: full design supply airflow (all systems) and (for VAV systems) at airflow with all VAV boxes at or near minimum position.
If airflow monitoring stations are provided, they can be used for these measurements.
Programming for preoccupancy purge and HVAC schedules are checked and certified as part of the acceptance requirements. The sequences are also required to be identified by specification section paragraph number (or drawing sheet number) in the compliance documents.
Demand controlled ventilation systems are checked for compliance with sensor location, calibration (either factory certificate or field validation) and tested for system response with both a high signal (produced by a certified calibration test gas applied to the sensor) and low signal (by increasing the set point above the ambient level). A certificate of acceptance must be provided to the enforcement agency that the demand control ventilation system meets the acceptance requirements for code compliance. The certificate of acceptance must include certification from sensor device manufacturers that their product will meet the requirements of §120.1(d)4F and will provide a signal that indicates the CO2 level is within range required by §120.1(d)4E; certification from the controls manufacturer that their product responds to the type of signal that the installed sensors supply and can be calibrated to the CO2 levels specified in §120.1(d)4E; and that the CO2 sensors have an accuracy within plus or minus 75 ppm at 600 and 1,000 ppm concentrations, and require calibration no more frequently than once every five years.